《高分子物理》课程教学资源(文献资料)Vanillin-Derived High-Performance Flame Retardant Epoxy Resins - Facile Synthesis and Properties

Macromolecules Article Vanillin-Derived High-Performance Flame Retardant Epoxy Resins: Facile Synthesis and Properties Sheng Wang Songqi Ma,Chenxiang Xu,Yuan Liu,Jinyue Dai,Zongbao Wang, Xiaoqing Liu,?Jing Chen,"Xiaobin Shen,Jingjing Wei,and Jin Zhu* of Ch 19A Yuquan Rd,Shijingshan District,Beijing 100049,P.R China ingbo iversity,Ningbo 315201,P.R China UL-94 VO etardant o- EP1,EP2Tg-214 applications 04 DGEBA Tr166℃ ies is challe stance are more diffi ult to be ac pape orus-hyd ogen ad dition I by re ing RA A wit dancy with UL4 Vo rating and high LOI of32 which ue to the utstandin dens cha dD2BAoStem ex 76.4 and ter vanillin-based epoxies are easy to be regulated by using INTRODUCTION 。arg and its d that have 30 esives,I ted circuit boa cks to d epory resin of the their exce adhesi d90 able o and cadan he epoxy resins are proid-based prop nol fully dep fossi ted into tely stable che prope ry16,2017 materials which have a wide of biomass Publi-hed。Fcbruay24201 189 C 0202090
Vanillin-Derived High-Performance Flame Retardant Epoxy Resins: Facile Synthesis and Properties Sheng Wang,†,‡ Songqi Ma,*,† Chenxiang Xu,†,‡ Yuan Liu,†,‡ Jinyue Dai,†,‡ Zongbao Wang,§ Xiaoqing Liu,† Jing Chen,† Xiaobin Shen,†,‡ Jingjing Wei,† and Jin Zhu*,† † Ningbo Institute of Materials Technology and Engineering, Chinese Academy of Sciences, 1219 Zhongguan West Road, Zhenhai District, Ningbo 315201, P. R. China ‡ University of Chinese Academy of Sciences, 19 A Yuquan Rd, Shijingshan District, Beijing 100049, P. R. China § Ningbo University, Ningbo 315201, P. R. China ABSTRACT: Lignin derivative vanillin when coupled with diamines and diethyl phosphite followed by reaction with echichlorohydrin yields high-performance flame retardant epoxy resins. Biorenewable and environment-friendly flame retardant alternatives to bisphenol A epoxy resins (having plenty of applications such as coatings, adhesives, composites, etc.) have captured great attention due to their ecological and economic necessity. Vanillin, an industrial scale monoaromatic compound from lignin, is a promising sustainable candidate for highperformance polymers, while synthesis of diepoxies is challenging. Meanwhile, bio-based epoxy resins combining high performance and excellent fire resistance are more difficult to be achieved. In this paper, two novel bio-based epoxy monomers EP1 and EP2 were synthesized by one-pot reaction containing Schiff base formation and phosphorus−hydrogen addition between vanillin, diamines, and diethyl phosphite, followed by reacting with epichlorohydrin. Their reactivities are similar to bisphenol A epoxy resin DGEBA. After curing they showed excellent flame retardancy with UL-94 V0 rating and high LOI of ∼32.8%, which was due to the outstanding intumescent and dense char formation ability. Meanwhile, it was found that the cured vanillin-based epoxies had exceedingly high Tgs of ∼214 °C, tensile strength of ∼80.3 MPa, and tensile modulus of ∼2709 MPa, much higher than the cured DGEBA with Tg of 166 °C, tensile strength of 76.4 MPa, and tensile modulus of 1893 MPa; the properties of vanillin-based epoxies are easy to be regulated by using different “coupling” agentsdiaminesduring the synthesis process. ■ INTRODUCTION Epoxy resins, as one of the three most important thermosetting polymers, have been widely employed in a multitude of fields such as coatings, adhesives, laminated circuit board, electronic component encapsulations, and advanced composites because of their excellent adhesion, chemical resistance, mechanical properties, and dielectric properties.1−5 Nowadays, almost all of the epoxy resins are produced from fossil resources, and 90% of the commercially available epoxy resins are diglycidyl ether of bisphenol A (DGEBA) via the reaction of bisphenol A with epichlorohydrin.6 Bisphenol A, fully dependent on fossil resources, accounts for greater than 67% of the molar mass of DGEBA.7 In addition, bisphenol A is a reprotoxic compound;8 and even if chemically incorporated into polymers, a small amount of bisphenol A can still release from the polymers with time due to the not completely stable chemical bonds linking bisphenol A.9 As a result, it is under close monitoring, and its application has been restricted in many countries. Recently, the finite and rising price of fossil resources, climate change from CO2 emission, and other environmental problems have raised interests in polymers from biorenewable raw materials which have a wide variety of biomass resources with low price and enhanced environment benefits. There are numerous bionewable resources including vegetable oils,10−14 cardanol,15 isosorbide,9,16 rosin,17,18 gallic acid,19−21 ferulic acid,22 lignin, and its derivatives23−26 that have been investigated as feedstocks for epoxy resins. Because of the long flexible aliphatic chain and low reactivity of internal epoxy groups, epoxidized vegetable oil and cardanol often exhibit poor thermal and mechanical properties.6,27 Although isosorbide, rosin, gallic acid, and ferulic acid-based epoxy resins exhibited satisfied thermal and mechanical properties, isosorbide-based one suffered from relatively high hydrophilicity,28 and rosin, gallic acid, and ferulic acid have seldom spare capacity due to their variety applications and limited resources. Lignin is the second most abundant natural organic material accounting for approximately 30% of organic carbon in the biosphere; it is also the only scalable renewable feedstock consisted of aromatic monomers,29 and it is highly underutilized.30 Epoxy resins directly from lignin exhibit several drawbacks such as slow curing rate, unstable properties, and issues with processability Received: January 16, 2017 Revised: February 20, 2017 Published: February 24, 2017 Article pubs.acs.org/Macromolecules © 2017 American Chemical Society 1892 DOI: 10.1021/acs.macromol.7b00097 Macromolecules 2017, 50, 1892−1901 Downloaded via GUANGDONG UNIV OF TECHNOLOGY on November 15, 2022 at 01:40:21 (UTC). See https://pubs.acs.org/sharingguidelines for options on how to legitimately share published articles
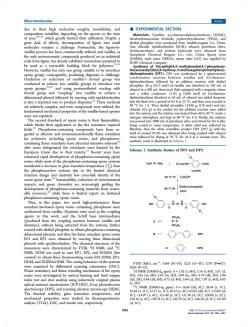
Macromolecules Article due to their high EXPERIMENTAL SECTION nich greatly limit ation.Despite Materials.Vanillin, molecules remains a challenge.Fo (EC) Co. the lignin-to ally utilize and ale from lignin.has al used o be i is challen is(( aethy44-methyienebi4,lpbelene dia osphi d in I5 groups using pe itol reacting with 2(013 mol) 11.838 s also reported way to produce diepo Thes me s h at 2 6g08m56ed to 8 their flan tato℃for8t0 ng g)wi polymers includin for 24 h in a v nd phosph svnthetic route is illustrated in Scheme 1 by th Scheme 1.Synthetic Routes of DPI and DP2 opean Unic years hav most of the ph ifested a dec HaN-R-NH2 2.2eqHO-CHO e in glass t nsition and -link density of th 40"C 1h C2HsOH ction of envir nent of phos ho e2 phosphte d report on in this high-pe ance flam ng 0 the base x- 9c。 cted wit te to n ph R=Q入Op EPI and EP2 wer obta ols with epic res DP2 NMR.DDM was used to sure EP1.EP2.and DGEBA EP by DSC) 8张m4364N-助30asO-H,12se-05 nd lim 4,88 h) ray ph y (SEM) stability,glass tnsitioa temperature,and nalysis (TGA),DSC.and tensile test
due to their high molecular weights, insolubility, and composition variability depending on the species or the time of year,30−32 which greatly limited their utilization. Despite a great deal of efforts, decomposition of lignin into small molecules remains a challenge. Fortunately, the lignin-tovanillin process has been commercially utilized, and vanillin, as the only monoaromatic compounds produced on an industrial scale from lignin, has already exhibited tremendous potential to be used as a renewable building block for polymers.33,34 However, vanillin has only one group suitable to be introduce epoxy group; consequently, producing diepoxies is challenge. Oxidation or reduction of vanillin’s formyl group was conducted to achieve two suitable groups to introduce two epoxy groups,25,26 and using pentaerythritol reacting with formyl group and “coupling” two vanillin to achieve a difunctional phenol followed by reacting with epichlorohydrin is also a reported way to produce diepoxies.23 These methods are relatively complex, and toxic compounds were utilized; the fundamental mechanical properties of the vanillin-based epoxies were not reported. The second drawback of epoxy resins is their flammability, which blocks their application in the fire resistance required fields.35 Phosphorus-containing compounds have been regarded as effective and environment-friendly flame retardants for polymers including epoxy resins, and phosphoruscontaining flame retardants have attracted intensive interests36 after some halogenated fire retardants were banned by the European Union due to their toxicity.37 Recent years have witnessed rapid development of phosphorus-containing epoxy resins, while most of the phosphorus-containing epoxy systems manifested a decrease in glass transition temperature (Tg) than the phosphorus-free systems due to the limited chemical structure design and relatively low cross-link density of the cured epoxy resin.38 Sustainability, reduction of environmental impacts, and green chemistry are increasingly guiding the development of phosphorus-containing materials from renewable resources,39 while there is limited report on biobased phosphorus-containing epoxy resins. Thus, in this paper, two novel high-performance flame retardant bio-based epoxy resins containing phosphorus were synthesized from vanillin. Diamines were used as the coupling agents in this work, and the Schiff base intermediates (produced from the coupling reaction between vanillin and diamines), without being extracted from the systems, further reacted with diethyl phosphite to obtain phosphorus-containing difunctional phenols; and then the flame retardant epoxy resins EP1 and EP2 were obtained by reacting these difunctianal phenols with epichlorohydrin. The chemical structures of the monomers were characterized by FTIR, 1 H NMR, and 13C NMR. DDM was used to cure EP1, EP2, and DGEBA (the control) to obtain three thermosetting resins EP1-DDM, EP2- DDM, and DGEBA-DDM. The curing behaviors of the systems were examined by differential scanning calorimetry (DSC). Flame retardancy and flame retarding mechanism of the epoxy resins were investigated by vertical burning and limit oxygen index test and char analysis using inductively coupled plasma optical emission spectrometer (ICP-OES), X-ray photoelectron spectroscopy (XPS), and scanning electron microscopy (SEM). The thermal stability, glass transition temperature, and mechanical properties were studied by thermogravimetric analysis (TGA), DSC, and tensile test, respectively. ■ EXPERIMENTAL SECTION Materials. Vanillin, 4,4-diaminodiphenylmethane (DDM), tetrabutylammonium bromide, p-phenylenediamine (PDA), and diethyl phosphite were purchased from Aladdin-reagent Co., China. Zinc chloride, epichlorohydrin (ECH), ethanol, petroleum ether, dichloromethane, and sodium hydroxide were obtained from Sinopharm Chemical Reagent Co., Ltd., China. Epoxy resin (DGEBA, trade name DER331, epoxy value 0.53) was supplied by DOW Chemical Company. Synthesis of Tetraethyl(4,4′-methylenebis(4,1-phenylene)- bis(azanediyl))bis((4-hydroxy-3-methoxyphenyl)methylene)- diphosphonate (DP1). DP1 was synthesized by a quintessential condensation reaction between vanillin and 4,4-diaminodiphenylmethane, followed by an addition reaction with diethyl phosphite. 20 g (0.13 mol) of vanillin was dissolved in 150 mL of ethanol in a 500 mL three-neck flask equipped with a magnetic stirrer and a reflux condenser. 11.83 g (0.06 mol) of 4,4-diaminodiphenylmethane dissolved in 50 mL of ethanol was added dropwise into the flask over a period of 0.5 h at 25 °C, and they were reacted at 40 °C for 1 h. Then diethyl phosphite (24.86 g, 0.18 mol) and zinc chloride (0.5 g) as the catalyst for the addition reaction were added into the system, and the mixture was heated from 40 to 80 °C under a nitrogen atmosphere and kept at 80 °C for 8 h. Finally, the mixture was poured into 1000 mL of petroleum ether and stirred for 0.5 h after being cooled to room temperature. A white solid was collected by filtration; then the white crystalline product DP1 (29.7 g) with the yield of around 93.3% was obtained after being washed with ethanol twice followed by drying at 70 °C for 24 h in a vacuum oven. The synthetic route is illustrated in Scheme 1. FTIR (KBr), cm−1 : 3364 (N−H); 3225 (O−H); 1278 (PO); 1026 (P−O). 1 H NMR (DMSO-d6, ppm): δ = 1.02 (t, 6H), 1.14 (t, 6H), 3.51 (d, 2H), 3.65 (m, 6H), 3.83 (m, 2H), 3.99 (m, 4H), 4.76 (dd, 2H), 5.96 (dd, 2H), 6.64 (dd, 6H), 6.75 (d, 4H), 6.84 (d, 2H), 7.07 (s, 4H), 8.85 (s, 2H). 13C NMR (DMSO-d6, ppm): δ = 16.68 (dd, 4C), 39.94 (s, 1C), 53.64 (s, 1C), 55.17 (s, 1C), 56.12 (s, 4C), 62.65 (dd, 2C), 113.09 (d, 2C), 114.07 (s, 4C), 115.40 (s, 2C), 121.38 (d, 2C), 128.00 (s, 2C), 129.18 (s, 4C), 130.78 (s, 2C), 145.76 (d, 2C), 146.34 (d, 2C), 147.69 (d, 2C). Scheme 1. Synthetic Routes of DP1 and DP2 Macromolecules Article DOI: 10.1021/acs.macromol.7b00097 Macromolecules 2017, 50, 1892−1901 1893
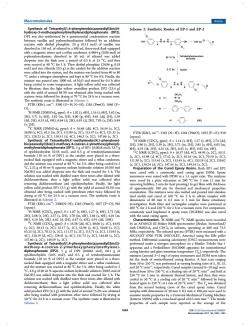
Macromolecules Article Synthesis ofTetrat-phemylenbs( Scheme 2.Synthetic Routes of EP-1 and EP-2 synt (2486g 018 5c霸NOH into the s h 40to89 onixog cldo pr 24 h in a vacuum R={入O》 m EP2 ,128.23 FTR(KBr,cm:3383(N-H1264(P=O方:1033(P-O910 13951(d 4C). 147 xy]p ate (EP1).sg of DI 1(0.005 .53.7 50.1 6.1 d to 13 24d27 5 (Soth EP d ep H Th. with d ed with DDMn a:l e M. then oduct EP1(.3 nfor hea 9 sion of 80 mm mm x3 mm for flam reta FTR(KB,cm:3300N-H01265(P=01027(P-0)910 (2 (dd 200 (m MR (CDO 46 NM Cl ppm): 9 and C NMR h DMS CDC ing at 400 ar 14702c21 s.4C).131.72(s,2C).144.48( (Ds e) DSC8000 de (10 wt of DP2)as the ed in a thre con nd 2 2 h. then a light yellow whn the rsported as the average of five
Synthesis of Tetraethyl(1,4-phenylenebis(azanediyl))bis((4- hydroxy-3-methoxyphenyl)methylene)diphosphonate (DP2). DP2 was also synthesized by a quintessential condensation reaction between vanillin and p-phenylenediamine followed by an addition reaction with diethyl phosphite. 20 g (0.13 mol) of vanillin was dissolved in 150 mL of ethanol in a 500 mL three-neck flask equipped with a magnetic stirrer and a reflux condenser. 6.4884 g (0.06 mol) of p-phenylenediamine dissolved in 50 mL of ethanol was added dropwise into the flask over a period of 0.5 h at 25 °C, and they were reacted at 40 °C for 1 h. Then diethyl phosphite (24.86 g, 0.18 mol) and zinc chloride (0.5 g) as the catalyst for the addition reaction were added into the system, and the mixture was heated from 40 to 80 °C under a nitrogen atmosphere and kept at 80 °C for 8 h. Finally, the mixture was poured into 1000 mL of H2O and stirred for 0.5 h after being cooled to room temperature. A light yellow solid was collected by filtration; then the light yellow crystalline product DP2 (23.4 g) with the yield of around 88.3% was obtained after being washed with acetone twice followed by drying at 70 °C for 24 h in a vacuum oven. The synthetic route is illustrated in Scheme 1. FTIR (KBr), cm−1 : 3390 (O−H, N−H); 1285 (PO); 1040 (P− O).1 H NMR (DMSO-d6, ppm): δ = 1.02 (t, 6H), 1.16 (t, 6H), 3.62 (m, 2H), 3.71 (s, 6H), 3.82 (m, 2H), 4.00 (p, 4H), 4.65 (dd, 2H), 5.39 (dd, 2H), 6.51 (d, 4H), 6.64 (d, 2H), 6.81 (d, 2H), 7.05 (s, 2H), 8.84 (s, 2H). 13C NMR (DMSO-d6, ppm): δ = 16.68 (dd, 4C), 54.54 (s, 2C), 56.08 (s, 4C), 62.5 (m, 2C), 112.99 (s, 2C), 115.37 (s, 4C), 121.32 (s, 2C), 128.23 (s, 2C), 139.51 (d, 4C), 146.2 (s, 2C), 147.66 (s, 2C). Synthesis of Tetraethyl(4,4′-methylenebis(4,1-phenylene)- bis(azanediyl))bis((3-methoxy-4-(oxiran-2-ylmethoxy)phenyl)- methylene)diphosphonate (EP1). 5 g of DP1 (0.0058 mol), 53.7 g of epichlorohydrin (0.58 mol), and 0.5 g of tetrabutylammonium bromide (10 wt % of DP1) as the catalyst were placed in a threenecked flask equipped with a magnetic stirrer and a reflux condenser, and the mixture was reacted at 80 °C for 3 h. After being cooled to 5 °C, 2.32 g of 40 wt % aqueous sodium hydroxide solution (0.058 mol NaOH) was added dropwise into the flask and reacted for 5 h. The solution was washed with distilled water three times after diluted with dichloromethane; then a light yellow solid was collected after removing dichloromethane and epichlorohydrin. Finally, the light yellow solid product EP1 (5.3 g) with the yield of around 93.5% was obtained after being washed with petroleum ether twice followed by drying at 50 °C for 24 h in a vacuum oven. The synthetic route is illustrated in Scheme 2. FTIR (KBr), cm−1 : 3300(N−H); 1265 (PO); 1027 (P−O); 910 (epoxy). 1 H NMR (CDCl3, ppm): δ = 1.07 (t, 6H), 1.27 (t, 6H), 2.72 (dd, 2H), 2.88 (t, 2H), 3.37 (s, 2H), 3.70 (m, 4H), 3.84 (s, 6H), 4.01 (m, 8H), 4.19 (dt, 2H), 4.62 (d, 2H), 6.47 (t, 4H), 6.91 (dd, 10H). 13C NMR (CDCl3, ppm): δ = 16.38 (dd, 4C), 40.06 (s, 1C), 44.92 (s, 2C), 50.13 (s, 2C), 55.17 (s, 1C), 55.96 (s, 4C), 56.68 (s, 1C), 63.23 (d, 2C), 70.12 (s, 2C), 111.37 (s, 2C), 113.71 (s, 2C), 113.93 (s, 4C), 120.19 (d, 4C), 129.41 (s, 4C), 131.72 (s, 2C), 144.48 (s, 2C), 147.60 (s, 2C), 149.59 (s, 2C). Synthesis of Tetraethyl(1,4-phenylenebis(azanediyl))bis((3- methoxy-4-(oxiran-2-ylmethoxy)phenyl)methylene)- diphosphonate (EP2). 5 g of DP2 (0.0065 mol), 60.1 g of epichlorohydrin (0.65 mol), and 0.5 g of tetrabutylammonium bromide (10 wt % of DP2) as the catalyst were placed in a threenecked flask equipped with a magnetic stirrer and a reflux condenser, and the mixture was reacted at 80 °C for 3 h. After being cooled to 5 °C, 2.6 g of 40 wt % aqueous sodium hydroxide solution (0.065 mol of NaOH) was added dropwise into the flask and reacted for 5 h. The solution was washed with distilled water three times after diluted with dichloromethane; then a light yellow solid was collected after removing dichloromethane and epichlorohydrin. Finally, the white solid product EP2 (4.3 g) with the yield of around 75.2% was obtained after being washed with petroleum ether twice followed by drying at 50 °C for 24 h in a vacuum oven. The synthetic route is illustrated in Scheme 2. FTIR (KBr), cm−1 : 3383 (N−H); 1264 (PO); 1033 (P−O); 910 (epoxy). 1 H NMR (CDCl3, ppm): δ = 1.14 (t, 6H), 1.27 (t, 6H), 2.74 (dd, 2H), 2.90 (t, 2H), 3.39 (s, 2H), 3.71 (m, 2H), 3.85 (s, 6H), 4.03 (m, 8H), 4.19 (dt, 2H), 4.55 (d, 2H), 6.43 (s, 4H), 6.92 (m, 6H). 13C NMR (CDCl3, ppm): δ = 16.37 (dd, 4C), 44.95 (s, 2C), 50.11 (s, 2C), 55.98 (d, 4C), 57.52 (s, 2C), 63.16 (m, 2C), 70.10 (s, 2C), 111.30 (s, 2C), 113.61 (s, 2C), 115.45 (s, 4C), 120.18 (d, 2C), 129.62 (s, 2C), 139.24 (d, 2C), 147.55 (s, 2C), 149.54 (s, 2C). Preparation of the Cured Epoxy Resins. Both EP1 and EP2 were cured with a commonly used curing agent DDM. Epoxy monomers were mixed with DDM in a 1:1 equiv ratio. The mixtures were cured by a plate vulcanizer at 200 °C for 3 min (1 min for removing bubbles, 2 min for heat pressing) to get films with thickness of approximately 100 μm for thermal and mechanical properties examination. The mixtures were also melted and poured into stainless steel molds and cured at 160 °C for 2 h to obtain samples with dimensions of 80 mm × 6.5 mm × 3 mm for flame retardancy investigation. Both films and rectangular samples were postcured at 200 °C for 2 h and 230 °C for 2 h in a vacuum oven. For comparison, commonly used bisphenol A epoxy resin (DGEBA) was also cured with the same curing agent. Characterization. 1 H NMR and 13C NMR spectra were recorded by an AVANCE III Bruker NMR spectrometer (Bruker, Switzerland) with DMSO-d6 and CDCl3 as solvents, operating at 400 and 75.5 MHz, respectively. The infrared spectra (FTIR) were measured with a NICOLET 6700 FTIR (NICOLET, America) using the KBr pellet method. Differential scanning calorimetry (DSC) measurements were performed under a nitrogen atmosphere on a Mettler Toledo Star 1 apparatus and a PerkinElmer DSC8000 apparatus for nonisothermal curing kinetics and glass transition temperature (Tg), respectively. The mixtures (around 3−5 mg) of epoxy monomers and DDM were taken for the study of nonisothermal curing kinetics. A heat scan ranging from 50 to 250 °C was performed at varying heating rates of 5, 10, 15, and 20 °C min−1 , respectively. Cured samples (around 8−10 mg) were heated from 50 to 250 °C at a heating rate of 20 °C min−1 and held at 250 °C for 3 min to eliminate thermal history, and then they were cooled to 50 °C at a cooling rate of 20 °C min−1 followed by being heated again to 250 °C at a rate of 20 °C min−1 . The Tg was obtained from the second heating curve of the cured epoxy resins. Cured samples with dimensions of 30 mm × 0.5 mm × 100 μm were used to examine tensile properties by a Universal Mechanical Testing Machine (Instron 5569A) with a cross-head speed of 0.5 mm min−1 . The tensile properties of each sample were reported as the average of five Scheme 2. Synthetic Routes of EP-1 and EP-2 Macromolecules Article DOI: 10.1021/acs.macromol.7b00097 Macromolecules 2017, 50, 1892−1901 1894
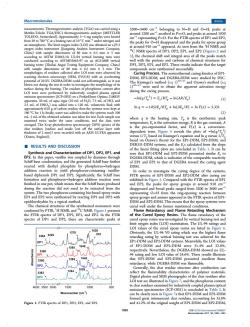
Macromolecules Article TGA/ analysis(TGA) rom 50 to 700 g rate the t (an 910cm 0 mm of DPL DP2 6.5m 3).the of all the aks n ns to 7 on an AGs 9 ere 20 kV.DGERA-DDM DDM,EP2-DDM,and DGEBA-DDM ere studied by DSC and 0awde od (ec of pl d during the curing process. (ICP Pe -ln(q/T')=E./RT,-ln(AR/E,) (1) ng=-1.052E,/RT+ln(AE,/R)-lnF(x)-5.33 5 mL of the oby The (XPS)s F(x)is with an AXIS ULTRA apparatus 1/7 for the EPI EP2-DDM RESULTS AND DISCUSSION DER331-DDM ss from the slo of the ed in Table 1.It car rapablereac diethy osphite by phosphoru system ls DPl and DP2 Signific tly the Schiff has and EP during the g0m3200o3600g EPI and EP2 were synthes ed by reacting DPI and DP2 with the ared in the DM.This ha the epoy systems were he N spectra of DPI and DP2.there are characteristic peaks ed by ver est and 026 1278 33643225 sy,中 ing vas th ighe EPI-DDN the 65 104 e300 the DCEBA-DDMo e UL A人 EPL-DDM 5%.Thes M 339 was DP2 126 the EP2、 ar res es afte 0035003000 500 in char res es examin (ICP-OES) mber (cm an be in Fig a that EP1-DDM d EP2-DD Figure 1.FTIR spectra of DP1,DP2,EP1,and EP2 and 412%of the priginal w ight of EPI-DDM and Ep2-DDM
measurements. Thermogravimetric analysis (TGA) was carried using a Mettler-Toledo TGA/DSC1 thermogravimetric analyzer (METTLER TOLEDO, Switzerland). Approximately 3−5 mg samples were heated from 50 to 700 °C at a heating rate of 10 °C min−1 under nitrogen and air atmospheres. The limit oxygen index (LOI) was obtained on a JF-3 oxygen index instrument (Jiangning Analysis Instrument Company, China) with sample dimensions of 80 mm × 6.5 mm × 3 mm according to ASTM D2863-10. UL-94 vertical burning tests were conducted according to ASTMD2863-97 on an AG5100B vertical burning tester (Zhuhai Angui Testing Equipment Company, China) with sample dimensions of 80 mm × 6.5 mm × 3 mm. The morphologies of residues collected after LOI tests were observed by scanning electron microscopy (SEM, EVO18) with an accelerating potential of 20 kV. DGEBA-DDM could not self-extinguish, so it was blown out during the test in order to investigate the morphology of its surface during the burning. The residues of phosphorus content after LOI tests were performed by inductively coupled plasma optical emission spectrometer (ICP-OES) on a PerkinElmer Optima 2100DV apparatus. 20 mL of aqua regia (10 mL of H2O, 7.5 mL of HCl, and 2.5 mL of HNO3) was added into a 120 mL volumetric flask with approximately 0.02 g of carbon residue; then the systems were kept at 180 °C for 1 h; finally, water was added to make the systems reach 100 mL. 5 mL of the obtained solution was taken for test. Each sample was examined twice under the same conditions, and the data were averaged. The X-ray photoelectron spectroscopy (XPS) spectra of the char residues (surface and inside (cut off the surface layer with thickness of 2 mm)) were recorded with an AXIS ULTRA apparatus (Kratos, England). ■ RESULTS AND DISCUSSION Synthesis and Characterization of DP1, DP2, EP1, and EP2. In this paper, vanillin was coupled by diamines through Schiff base condensation, and the generated Schiff base further reacted with diethyl phosphite by phosphorus−hydrogen addition reaction to yield phosphorus-containing vanillinbased diphenols DP1 and DP2. Significantly, the Schiff base formation and phosphorus−hydrogen addition reaction were finished in one pot, which means that the Schiff bases produced during the reaction did not need to be extracted from the system. The two phosphorus-containing bio-based epoxy resins EP1 and EP2 were synthesized by reacting DP1 and DP2 with epichlorohydrin by a typical method. The chemical structures of the synthesized monomers were confirmed by FTIR, 1 H NMR, and 13C NMR. Figure 1 presents the FTIR spectra of DP1, DP2, EP1, and EP2. In the FTIR spectra of DP1 and DP2, there are characteristic peaks at 3200−3400 cm−1 belonging to N−H and O−H, peaks at around 1280 cm−1 ascribed to PO, and peaks at around 1030 cm−1 representing P−O. For the FTIR spectra of EP1 and EP2, the peaks for O−H disappeared and the peaks for epoxy group at around 910 cm−1 appeared. As seen from the 1 H NMR and 13C NMR spectra of DP1, DP2, EP1, and EP2 (Figures 2 and 3), the chemical shift and integral area of all the peaks match well with the protons and carbons of chemical structures for DP1, DP2, EP1, and EP2. These results indicate that the target compounds were synthesized successfully. Curing Process. The nonisothermal curing kinetics of EP1- DDM, EP2-DDM, and DGEBA-DDM were studied by DSC. The Kissinger’s method (eq 1) 40−42 and Ozawa’s method (eq 2) 40−43 were used to obtain the apparent activation energy during the curing process. − =− ln( / ) / ln( / ) q T E RT AR E p 2 ap a (1) ln 1.052 / ln( / ) ln ( ) 5.331 q E RT AE R F x =− + − − ap a (2) where q is the heating rate, Tp is the exothermic peak temperature, Ea is the activation energy, R is the gas constant, A is the pre-exponential factor, and F(x) is a conversiondependent term. Figure 4 reveals the plots of −ln(q/Tp 2 ) versus 1/Tp based on Kissinger’s equation and ln q versus 1/Tp based on Ozawa’s theory for the EP1-DDM, EP2-DDM, and DER331-DDM systems, and the Eas calculated from the slope of the linear fitting plots are concluded in Table 1. It can be seen that EP1-DDM and EP2-DDM presented similar Ea to DGEBA-DDM, which is indicative of the comparable reactivity of EP1 and EP2 to that of DGEBA toward the curing agent DDM. In order to investigate the curing degree of the systems, FITR spectra of EP1-DDM and EP2-DDM after curing are exhibited in Figure 5. Compared with the FTIR spectra of EP1 and EP2, the peaks for epoxy groups at around 910 cm−1 disappeared and broad peaks ranged from 3200 to 3600 cm−1 representing O−H from the ring-opening reaction between epoxy groups and amines appeared in the FTIR spectra of EP1- DDM and EP2-DDM. This means that the epoxy systems were cured well under the former mentioned conditions. Flame Retardancy and Flame Retarding Mechanism of the Cured Epoxy Resins. The flame retardancy of the cured epoxy resins was investigated by vertical burning test and limit oxygen index (LOI) examination. The UL-94 ratings and LOI values of the cured epoxy resins are listed in Figure 6. Obviously, the UL-94 V0 rating which was the highest flame retarding rating by vertical burning test was achieved for the EP1-DDM and EP2-DDM systems. Meanwhile, the LOI values of EP1-DDM and EP2-DDM were 31.4% and 32.8%, respectively. Nevertheless, the DGEBA-DDM showed no UL- 94 rating and low LOI value of 24.6%. These results illustrate that EP1-DDM and EP2-DDM presented excellent flame retardancy, while DGEBA-DDM was flammable. Generally, the char residue structure after combustion can reflect the flammability characteristics of polymer materials. Digital photos and SEM photographs of the char residues after LOI test are illustrated in Figure 7, and the phosphorus content in char residues examined by inductively coupled plasma optical emission spectrometer (ICP-OES) is concluded in Table 2. It can be clearly seen in Figure 7a that EP1-DDM and EP2-DDM formed great intumescent char residues, accounting for 35.8% Figure 1. FTIR spectra of DP1, DP2, EP1, and EP2. and 41.2% of the original weight of EP1-DDM and EP2-DDM, Macromolecules Article DOI: 10.1021/acs.macromol.7b00097 Macromolecules 2017, 50, 1892−1901 1895
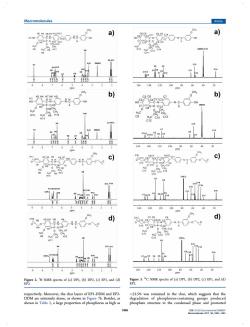
Macromolecules Article a) a) es CHa 。 b) b) CBO-P-OC N-g广ow cc品c2 7h 销室销 6% G) ceeHao 64 d) e程 d) 40 品8 e“ae 2 16011201000020 e2()P,间D2同p, show proportion of phosphorus ashigh as 8ct0eo2.a2T
respectively. Moreover, the char layers of EP1-DDM and EP2- DDM are extremely dense, as shown in Figure 7b. Besides, as shown in Table 2, a large proportion of phosphorus as high as ∼53.5% was remained in the char, which suggests that the degradation of phosphorus-containing groups produced phosphate structure in the condensed phase and promoted Figure 2. 1 H NMR spectra of (a) DP1, (b) DP2, (c) EP1, and (d) EP2. Figure 3. 13C NMR spectra of (a) DP1, (b) DP2, (c) EP1, and (d) EP2. Macromolecules Article DOI: 10.1021/acs.macromol.7b00097 Macromolecules 2017, 50, 1892−1901 1896
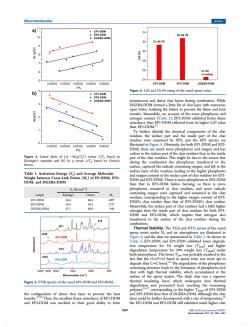
Macromolecules Article a)" 32 26 24 0.0225002300002350.002400.00245 EP1-DDM 1/Te b)4 Figure6.LOI ad UL rating of the cured epory resin of the more phe ohorus and thanp-DDM reflected from tts hgher LOI value a。o paboof the harredu thae DDM, 飘 This might tbe due to theres and left in th Table DDM,and DGEBA-DDM E.(kl mor) and rem EPI-DDM tent of EP2 604 19 esidue EP2-DDM Stability.The TGA and DTG of the cured poxy resins under N:and air atm Ta1-DDM and EPDDM ed lower and was pro ably a ed to th de than c C bor on of the 0003500300 cmulated at the ace epox Figure 5.FTIR spectra of the cured EP1-DDM and EP2-DDM. which degradation and prevented heat reachi ng the EPL-DM and EP2-DDM was ascribed to their good ability to form the EP1-DDMad EP2-DDMstill ehbited much higher char
the configuration of dense char layer to prevent the heat transfer.35,44 Thus, the excellent flame retardancy of EP1-DDM and EP2-DDM was ascribed to their good ability to form intumescent and dense char layers during combustion. While DGEBA-DDM formed a litter bit of char layer with numerous open holes, verifying the failure to prevent the flame and heat transfer. Meanwhile, on account of the more phosphorus and nitrogen content (Table 2), EP2-DDM exhibited better flame retardancy than EP1-DDM reflected from its higher LOI value than EP1-DDM.45 To further identify the chemical components of the char residues, the surface part and the inside part of the char residues were examined by XPS, and the XPS spectra are illustrated in Figure 8. Obviously, for both EP1-DDM and EP2- DDM, there are much more phosphorus and oxygen and less carbon in the surface part of the char residues than in the inside part of the char residues. This might be due to the reason that during the combustion the phosphorus transferred to the surface, captured the radicals containing oxygen, and left in the surface layer of the residues, leading to the higher phosphorus and oxygen content in the surface part of char residues for EP1- DDM and EP2-DDM. There is more phosphorus in EP2-DDM than that in EP1-DDM before burning, so there is more phosphorus remained in char residues, and more radicals containing oxygen were captured and remained in the char residues, corresponding to the higher oxygen content of EP2- DDM’s char residue than that of EP1-DDM’s char residue. Meanwhile, the surface part of char residues had a little higher nitrogen than the inside part of char residues for both EP1- DDM and EP2-DDM, which implies that nitrogen also transferred to the surface of the char residues during the combustion. Thermal Stability. The TGA and DTG curves of the cured epoxy resins under N2 and air atmospheres are illustrated in Figure 9, and the data are summarized in Table 3. As shown in Table 3, EP1-DDM and EP2-DDM exhibited lower degradation temperature for 5% weight loss (Td5%) and higher degradation temperature for 30% weight loss (Td30%) under both atmospheres. The lower Td5% was probably ascribed to the fact that the OP−O bond in epoxy resin was more apt to degrade than C−C bond.46 The degradation of the phosphorus containing structure leads to the formation of phosphorus-rich char with high thermal stability, which accumulated at the surface of the epoxy matrix. The thick char was a superior thermal insulating layer, which undergone slow thermal degradation and prevented heat reaching the remaining polymer,44,47 corresponding to the higher Td30% of EP1-DDM and EP2-DDM than that of DGEBA-DDM. Although the char layer could be further decomposed with a rise of temperature,48 the EP1-DDM and EP2-DDM still exhibited much higher char Figure 4. Linear plots of (a) −ln(q/Tp 2 ) versus 1/Tp based on Kissinger’s equation and (b) ln q versus 1/Tp based on Ozawa’s theory. Table 1. Activation Energy (Ea) and Average Molecular Weight between Cross-Link Points (Mc) of EP-DDM, EP2- DDM, and DGEBA-DDM Ea (kJ mol−1 ) sample Kissinger Ozawa Mc EP1-DDM 56.4 60.4 1907 EP2-DDM 54.4 58.5 1727 DGEBA-DDM 57.1 60.9 944 Figure 5. FTIR spectra of the cured EP1-DDM and EP2-DDM. Figure 6. LOI and UL-94 rating of the cured epoxy resins. Macromolecules Article DOI: 10.1021/acs.macromol.7b00097 Macromolecules 2017, 50, 1892−1901 1897

Macromolecules Article a) b) 01修 9% 11% EP1-DDM EP1-DDM surface EP2-DDM inside EP2-DDM surace 0 60 400 200 EP2 DDM resulted in the high char yields.The lower under ai attributed to the third sta than that of phosphorus content should lead to of the DDM DGEBA-DDM and DGEBA-DDM of183 d214℃, rely,tha e cr nd th The nt are the sing eq 3. M.="Mp+DMMpDM (3) nd M represent in the As ith R re t d EP. ibited highe Ms than ogen atm osphere.As m vio the phospho densi DD oh- mainly resulted from the higher rigidity of EP1-DDM and EP2- Table 2.Phosphorus and Nitrogen Content of EP-DDM,EP2-DDM,and DGEBA-DDM before and after Burning (wt $6)phospl GEBA-DD. 89 8060h22a2a
yield at 700 °C (R700) as high as ∼44.7% under air atmosphere and ∼58% under a nitrogen atmosphere than DEGBA-DDM with R700 of 0% under air atmosphere and 14.0% under a nitrogen atmosphere. As mentioned previously, the phosphonate group as a promoter for “char formation” formed the phosphorus-rich layer during the degradation process, which resulted in the high char yields. The lower R700 under air atmosphere than that under a nitrogen atmosphere was attributed to the third stage degradation belonging to the oxidative degradation of residual carbon under air atmosphere, which can be seen in Figure 9. Meanwhile, the phosphorus content of EP2-DDM is higher than that of EP1-DDM, resulting in its higher Td30% and R700 than EP1-DDM. Higher phosphorus content should lead to lower Td5% of the phosphorus-containing systems, while EP2-DDM showed higher Td5% than EP1-DDM. Our previous work proved that increasing the cross-link density can improve the initial degradation temperature.38 EP2-DDM has higher cross-link density relative to EP1-DDM, which corresponds to its higher Td5% than EP1-DDM. Glass Transition Temperature of the Cured Epoxy Resins. Glass transition temperature (Tg) is a major parameter for thermosetting materials. The Tgs of EP1-DDM, EP2-DDM, and DGEBA-DDM were determined by DSC, and the results are summarized in Figure 10. EP1-DDM and EP2-DDM showed higher Tgs of 183 and 214 °C, respectively, than DGEBA-DDM with Tg of 166 °C. The Tgs of the cross-linked polymers have a close tie with their cross-link density and the rigidity of the chain segment structure.49,50 The higher the cross-link density of the thermosets and rigidity of their chain segment are the higher the Tg is. In order to estimate the crosslink density of the cured epoxy resins, the average molecular weight between cross-link points (Mc) (Table 1) was calculated using eq 3. = + M nM n M n c EP EP DDM DDM DDM (3) where n and M represent the molarity and molar mass of the corresponding component in the epoxy formulations.51 As shown in Table 1, EP1-DDM and EP2-DDM exhibited higher Mcs than DGEBA-DDM, which means that they possessed lower cross-link density than DGEBA-DDM. Thus, the higher Tgs of EP1-DDM and EP2-DDM than that of DGEBA-DDM mainly resulted from the higher rigidity of EP1-DDM and EP2- Figure 7. (a) Digital photos and (b) SEM photographs of the residues after LOI test. Table 2. Phosphorus and Nitrogen Content of EP-DDM, EP2-DDM, and DGEBA-DDM before and after Burning before burning after burning sample phosphorus content (wt %) nitrogen content (wt %) weight residue (wt %) phosphorus content (wt %) phosphorus retention (%) EP1-DDM 6.50 4.40 35.8 6.99 38.5 EP2-DDM 7.18 4.86 41.2 9.32 53.5 DGEBA-DDM 0 2.86 Figure 8. XPS spectra of the surface part and inside part of the char residues of EP1-DDM and EP2-DDM. Macromolecules Article DOI: 10.1021/acs.macromol.7b00097 Macromolecules 2017, 50, 1892−1901 1898
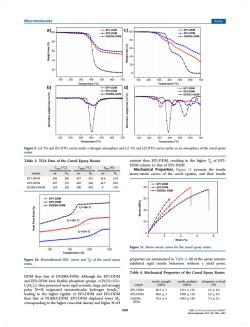
Macromolecules Aricle 88cm 主8 20 200 00 200 70 d 1020 200 30040 reo0 ()()G m Table 3.TGA Data of the Cured Epoxy Resins Tas("c) Tao (C) R(%) Mechanical Prop ERLDDM 340427435 266 353 447 20 =2140 2 turo (C) 20 Figure 11.Stress-strain curves for the cured epoxy resins. otheral DSC curves and T of the cured epory Table 4.Mechanical Properties of the Cured Epoxy Resins P2-DDM nding to the highe density and higher NH 8cna
DDM than that of DGEBA-DDM. Although the EP1-DDM and EP2-DDM have flexible phosphate groups −(P(O)−(O− C2H5)2), they possessed more rigid aromatic rings and strongly polar N−H originated intramolecular hydrogen bonds,52 leading to the higher rigidity of EP1-DDM and EP2-DDM than that of DGEBA-DDM. EP2-DDM displayed lower Mc, corresponding to the higher cross-link density and higher N−H content than EP1-DDM, resulting in the higher Tg of EP2- DDM relative to that of EP1-DDM. Mechanical Properties. Figure 11 presents the tensile stress−strain curves of the cured epoxies, and their tensile properties are summarized in Table 4. All of the epoxy systems exhibited rigid tensile behaviors without a yield point. Figure 9. (a) TG and (b) DTG curves under a nitrogen atmosphere and (c) TG and (d) DTG curves under an air atmosphere of the cured epoxy resins. Table 3. TGA Data of the Cured Epoxy Resins Td5% (°C) Td30% (°C) R700 (%) sample air N2 air N2 air N2 EP1-DDM 286 340 427 435 26.6 53.0 EP2-DDM 287 353 482 450 44.7 58.0 DGEBA-DDM 356 382 390 403 0 14.0 Figure 10. Nonisothermal DSC curves and Tgs of the cured epoxy resins. Figure 11. Stress−strain curves for the cured epoxy resins. Table 4. Mechanical Properties of the Cured Epoxy Resins sample tensile strength (MPa) tensile modulus (MPa) elongation at break (%) EP1-DDM 80.3 ± 5 2114 ± 132 5.2 ± 0.4 EP2-DDM 60.6 ± 3 2709 ± 110 2.6 ± 0.2 DGEBADDM 76.4 ± 6 1893 ± 140 7.4 ± 0.5 Macromolecules Article DOI: 10.1021/acs.macromol.7b00097 Macromolecules 2017, 50, 1892−1901 1899
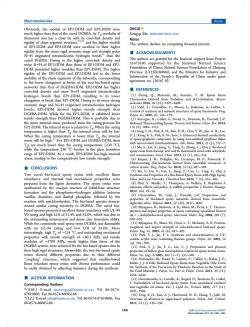
Macromolecules Article the ORCID tha tha Songqi Ma:000-0002.9652-1016 H ■ACKNOWLEDGMENTS cial s EP2 theP-DM the highe mobility of the chain seg bio-hased kthahofDGEBA-DDM.EP2-DDM has ■REFERENCES den P-DDM.wing to strong a A-DDM he. al stre oduced from the ess fo H rk,K H;Kim,B.H;Choi,Y.W;Jun,G.H.;Le D B.S.;P Aa,AMt.2013,25S,7 much lowe 230 the t ture (230 C) 5)M EP2-DDM.A EP2-DDM high stress leading to the comp aratively low tensile strength ■CONCLUSIONS gPom5a.2010,35(4),487-s09 nd Low (2)555-S the h (8)Fh nation and the additio hite,followed by the DGEBA The c dyl ether.Po 620 ed b 201l,52(16,3611 ith no UL. 94 rating low L0Iof24.6% ased epoxy 200 49 1g9 803MP and t resin 270 her than those 13 igid le.the two bic perties he ed that lin ba M:P ate,V.Caillol,Habas,J.P. epoxy divers n,J.J.A esin hom veget ng PP A Pol Chem 201.( ■AUTHOR INFORMATION ding authors (S.M.)E-mail mas mte.ac.cni Tel 86-0574. able oil amine.Eur..Lipid Sci Technol 2015,117(11) *0Z)E T86-057487619806Fax 86-0574-86685186. 2011,22(0.139-150. sug 90
Obviously, the moduli of EP1-DDM and EP2-DDM were much higher than that of the cured DGEBA. As Tg, modulus of thermoset also has a close tie with its cross-link density and rigidity of chain segment structure,49,50 and the higher moduli of EP1-DDM and EP2-DDM were ascribed to their higher rigidity from the more rigid aromatic rings and strongly polar N−H originated intramolecular hydrogen bonds52 than the cured DGEBA. Owing to the higher cross-link density and more N−H of EP2-DDM than those of EP1-DDM and EP2- DDM presented higher modulus than EP1-DDM. The higher rigidity of the EP1-DDM and EP2-DDM led to the lower mobility of the chain segments of the networks, corresponding to the lower elongation at break of the two bio-based epoxy networks than that of DGEBA-DDM. EP2-DDM has higher cross-link density and more N−H originated intramolecular hydrogen bonds than EP1-DDM, resulting in its lower elongation at break than EP1-DDM. Owing to its more strong aromatic rings and N−H originated intramolecular hydrogen bonds, EP1-DDM showed higher tensile strength than DGEBA-DDM. While for the EP2-DDM, it exhibited lower tensile strength than DGEBA-DDM. This is probably due to the more internal stress produced from the curing process for EP2-DDM. The internal stress is related to Tg. When the curing temperature is higher than Tg, the internal stress will be low. When the curing temperature is lower than Tg, the internal stress will be high.53 For EP1-DDM and DGEBA-DDM, their Tgs are much lower than the curing temperature (230 °C), while the temperature 230 °C locates in the glass transition range of EP2-DDM. As a result, EP2-DDM has high internal stress, leading to the comparatively low tensile strength. ■ CONCLUSIONS Two novel bio-based epoxy resins with excellent flame retardancy and thermal and mechanical properties were prepared from the lignin derivative. The epoxy resins were synthesized by the one-pot reaction of Schiff-base structure formation and the phosphorus−hydrogen addition between vanillin, diamines, and diethyl phosphite, followed by the reaction with epichlorohydrin. The bio-based epoxies demonstrated similar curing reactivity to DGEBA. The cured biobased epoxies presented excellent flame retardancy with UL-94 V0 rating and high LOI of 31.4% and 32.8%, which was due to the outstanding intumescent and dense char formation ability. While the commonly used epoxy resin DGEBA was flammable with no UL-94 rating and low LOI of 24.6%. More interestingly, high Tg of ∼214 °C and outstanding mechanical properties with tensile strength of ∼80.3 MPa and tensile modulus of ∼2709 MPa, much higher than those of the DGEBA system, were achieved for the bio-based epoxies due to their high rigid structures. Meanwhile, the two bio-based epoxy resins showed different properties due to their different “coupling” structure, which suggested that vanillin-based flame retardant epoxy resins with diverse performance could be easily obtained by adjusting diamines during the synthesis. ■ AUTHOR INFORMATION Corresponding Authors *(S.M.) E-mail masongqi@nimte.ac.cn; Tel 86-0574- 87619806; Fax 86-0574-86685186. *(J.Z.) E-mail jzhu@nimte.ac.cn; Tel 86-0574-87619806; Fax 86-0574-86685186. ORCID Songqi Ma: 0000-0002-9652-1016 Notes The authors declare no competing financial interest. ■ ACKNOWLEDGMENTS The authors are grateful for the financial support from Project 51473180 supported by the National Natural Science Foundation of China, Natural Science Foundation of Zhejiang Province (LY15E030004), and the Ministry for Industry and Information of the People’s Republic of China under grant agreement no. [2016] 92. ■ REFERENCES (1) Zhang, Q.; Molenda, M.; Reineke, T. M. Epoxy Resin Thermosets Derived from Trehalose and β-Cyclodextrin. Macromolecules 2016, 49 (22), 8397−8406. (2) Vidil, T.; Tournilhac, F.; Musso, S.; Robisson, A.; Leibler, L. Control of reactions and network structures of epoxy thermosets. Prog. Polym. Sci. 2016, 62, 126−179. (3) Auvergne, R.; Caillol, S.; David, G.; Boutevin, B.; Pascault, J.-P. Biobased Thermosetting Epoxy: Present and Future. Chem. Rev. 2014, 114 (2), 1082−1115. (4) Song, S. H.; Park, K. H.; Kim, B. H.; Choi, Y. W.; Jun, G. H.; Lee, D. J.; Kong, B. S.; Paik, K. W.; Jeon, S. Enhanced thermal conductivity of epoxy-graphene composites by using non-oxidized graphene flakes with non-covalent functionalization. Adv. Mater. 2013, 25 (5), 732−7. (5) Ma, S.; Liu, X.; Jiang, Y.; Tang, Z.; Zhang, C.; Zhu, J. Bio-based epoxy resin from itaconic acid and its thermosets cured with anhydride and comonomers. Green Chem. 2013, 15 (1), 245−254. (6) Raquez, J. M.; Deleglise, M.; Lacrampe, M. F.; Krawczak, P. ́ Thermosetting (bio)materials derived from renewable resources: A critical review. Prog. Polym. Sci. 2010, 35 (4), 487−509. (7) Ma, S.; Liu, X.; Fan, L.; Jiang, Y.; Cao, L.; Tang, Z.; Zhu, J. Synthesis and Properties of a Bio-Based Epoxy Resin with High Epoxy Value and Low Viscosity. ChemSusChem 2014, 7 (2), 555−562. (8) Flint, S.; Markle, T.; Thompson, S.; Wallace, E. Bisphenol A exposure, effects, and policy: A wildlife perspective. J. Environ. Manage. 2012, 104, 19−34. (9) Chrysanthos, M.; Galy, J.; Pascault, J.-P. Preparation and properties of bio-based epoxy networks derived from isosorbide diglycidyl ether. Polymer 2011, 52 (16), 3611−3620. (10) Miyagawa, H.; Mohanty, A. K.; Misra, M.; Drzal, L. T. Thermophysical and impact properties of epoxy containing epoxidized linseed oil, 1 - Anhydride-cured epoxy. Macromol. Mater. Eng. 2004, 289 (7), 629−635. (11) Miyagawa, H.; Misra, M.; Drzal, L. T.; Mohanty, A. K. Fracture toughness and impact strength of anhydride-cured biobased epoxy. Polym. Eng. Sci. 2005, 45 (4), 487−495. (12) Park, S. J.; Jin, F. L. Synthesis and characterization of UVcurable acrylic resin containing fluorine groups. Polym. Int. 2005, 54 (4), 705−709. (13) Park, S. J.; Jin, F. L.; Lee, C. J. Preparation and physical properties of hollow glass microspheres-reinforced epoxy matrix resins. Mater. Sci. Eng., A 2005, 402 (1−2), 335−340. (14) Stemmelen, M.; Pessel, F.; Lapinte, V.; Caillol, S.; Habas, J. P.; Robin, J. J. A Fully Biobased Epoxy Resin from Vegetable Oils: From the Synthesis of the Precursors by Thiol-ene Reaction to the Study of the Final Material. J. Polym. Sci., Part A: Polym. Chem. 2011, 49 (11), 2434−2444. (15) Dworakowska, S.; Cornille, A.; Bogdał, D.; Boutevin, B.; Caillol, S. Formulation of bio-based epoxy foams from epoxidized cardanol and vegetable oil amine. Eur. J. Lipid Sci. Technol. 2015, 117 (11), 1893−1902. (16) Feng, X. H.; East, A. J.; Hammond, W. B.; Zhang, Y.; Jaffe, M. Overview of advances in sugar-based polymers. Polym. Adv. Technol. 2011, 22 (1), 139−150. Macromolecules Article DOI: 10.1021/acs.macromol.7b00097 Macromolecules 2017, 50, 1892−1901 1900

Macromolecules Article (7) biobased epox (3)mly,N;Fache,M:Minard,R;Negrell,C:Callol,David.G u. 2015,6(35).62576291 unds:the state of the Q:Hu Zhang ration of a (40)o,D of pe ed b 19)Aouf,C Lecomte,J Villen 20283t P-Duh Li,P.;Sui,G;Yu,Yi Li,G;Yang Xi Ryu,S.Cur 36 has,H:Fache,M:Caillol,Boutevin,B. m人2013,98i a nove (43)W ed the 006.91(8.174 1754 rd,R Caillo,Allais,F.Ferulic ab wheat bra 7,9583 23K0 o,Y.S dem Wod m (4).701 14,99, 46) u.H.: u,Y.A ef in,B.:Caillol.S (26)Fac (01.526 M;Au X.:Hu.Y die ng W;Lu H.Th 2011,92(0.164 TG-FTIR and DP.MS. 49)】 High-Perfo y n() i Jabe 01 ia22016,49(0 337(60 (51)Xie,T A M SD o。227 52)Liu,H.:Xu,K:Cai,H.:Su,I:Liu,X:Fu,Z:Chen,M.Therma Schift-base .Po 009,306,1316-1323. 33)Fachd M;Bo (35L,Y.LF r0m20i4,16(4, el phosphorus 200142(8.3445-3454 36)Qian,X;So L:B their pe me reta 07()379 10
(17) Liu, X. Q.; Zhang, J. W. High-performance biobased epoxy derived from rosin. Polym. Int. 2010, 59 (5), 607−609. (18) Liu, X. Q.; Huang, W.; Jiang, Y. H.; Zhu, J.; Zhang, C. Z. Preparation of a bio-based epoxy with comparable properties to those of petroleum-based counterparts. eXPRESS Polym. Lett. 2012, 6 (4), 293−298. (19) Aouf, C.; Lecomte, J.; Villeneuve, P.; Dubreucq, E.; Fulcrand, H. Chemo-enzymatic functionalization of gallic and vanillic acids: synthesis of bio-based epoxy resins prepolymers. Green Chem. 2012, 14 (8), 2328−2336. (20) Aouf, C.; Nouailhas, H.; Fache, M.; Caillol, S.; Boutevin, B.; Fulcrand, H. Multi-functionalization of gallic acid. Synthesis of a novel bio-based epoxy resin. Eur. Polym. J. 2013, 49 (6), 1185−1195. (21) Cao, L.; Liu, X.; Na, H.; Wu, Y.; Zheng, W.; Zhu, J. How a biobased epoxy monomer enhanced the properties of diglycidyl ether of bisphenol A (DGEBA)/graphene composites. J. Mater. Chem. A 2013, 1 (16), 5081−5088. (22) Menard, R.; Caillol, S.; Allais, F. Ferulic acid-based renewable ́ esters and amides-containing epoxy thermosets from wheat bran and beetroot pulp: Chemo-enzymatic synthesis and thermomechanical properties characterization. Ind. Crops Prod. 2017, 95, 83−95. (23) Koike, T. Progress in Development of Epoxy Resin Systems Based on Wood Biomass in Japan. Polym. Eng. Sci. 2012, 52 (4), 701− 717. (24) Zhao, B.; Chen, G.; Liu, Y.; Hu, K.; Wu, R. Synthesis of lignin base epoxy resin and its characterization. J. Mater. Sci. Lett. 2001, 20 (9), 859−862. (25) Fache, M.; Viola, A.; Auvergne, R.; Boutevin, B.; Caillol, S. Biobased epoxy thermosets from vanillin-derived oligomers. Eur. Polym. J. 2015, 68 (0), 526−535. (26) Fache, M.; Auvergne, R.; Boutevin, B.; Caillol, S. New vanillinderived diepoxy monomers for the synthesis of biobased thermosets. Eur. Polym. J. 2015, 67, 527−538. (27) Chrysanthos, M.; Galy, J.; Pascault, J.-P. Influence of the BioBased Epoxy Prepolymer Structure on Network Properties. Macromol. Mater. Eng. 2013, 298 (11), 1209−1219. (28) Łukaszczyk, J.; Janicki, B.; Kaczmarek, M. Synthesis and properties of isosorbide based epoxy resin. Eur. Polym. J. 2011, 47 (8), 1601−1606. (29) Tuck, C. O.; Perez, E.; Horva ́ th, I. T.; Sheldon, R. A.; Poliakoff, ́ M. Valorization of Biomass: Deriving More Value from Waste. Science 2012, 337 (6095), 695−699. (30) Upton, B. M.; Kasko, A. M. Strategies for the Conversion of Lignin to High-Value Polymeric Materials: Review and Perspective. Chem. Rev. 2016, 116 (4), 2275−2306. (31) Hofmann, K.; Glasser, W. Engineering plastics from lignin, 23. Network formation of lignin-based epoxy resins. Macromol. Chem. Phys. 1994, 195 (1), 65−80. (32) Hofmann, K.; Glasser, W. G. Engineering Plastics from Lignin. 22. Cure of Lignin Based Epoxy Resins. J. Adhes. 1993, 40 (2−4), 229−241. (33) Fache, M.; Boutevin, B.; Caillol, S. Vanillin, a key-intermediate of biobased polymers. Eur. Polym. J. 2015, 68, 488−502. (34) Fache, M.; Darroman, E.; Besse, V.; Auvergne, R.; Caillol, S.; Boutevin, B. Vanillin, a promising biobased building-block for monomer synthesis. Green Chem. 2014, 16 (4), 1987−1998. (35) Liu, Y. L. Flame-retardant epoxy resins from novel phosphoruscontaining novolac. Polymer 2001, 42 (8), 3445−3454. (36) Qian, X.; Song, L.; Bihe, Y.; Yu, B.; Shi, Y.; Hu, Y.; Yuen, R. K. Organic/inorganic flame retardants containing phosphorus, nitrogen and silicon: preparation and their performance on the flame retardancy of epoxy resins as a novel intumescent flame retardant system. Mater. Chem. Phys. 2014, 143 (3), 1243−1252. (37) The European Parliament and the European Council: Off. J. Eur. Union, 2003, Directive 2002/96/EC of 27. (38) Ma, S.; Liu, X.; Jiang, Y.; Fan, L.; Feng, J.; Zhu, J. Synthesis and properties of phosphorus-containing bio-based epoxy resin from itaconic acid. Sci. China: Chem. 2014, 57 (3), 379−388. (39) Illy, N.; Fache, M.; Menard, R.; Negrell, C.; Caillol, S.; David, G. ́ Phosphorylation of bio-based compounds: the state of the art. Polym. Chem. 2015, 6 (35), 6257−6291. (40) Rosu, D.; Cas ̧ caval, C.; Mustata ̧ , F.; Ciobanu, C. Cure kinetics of ̌ epoxy resins studied by non-isothermal DSC data. Thermochim. Acta 2002, 383 (1), 119−127. (41) Cai, H.; Li, P.; Sui, G.; Yu, Y.; Li, G.; Yang, X.; Ryu, S. Curing kinetics study of epoxy resin/flexible amine toughness systems by dynamic and isothermal DSC. Thermochim. Acta 2008, 473 (1−2), 101−105. (42) Wang, C. S.; Lin, C. H. Properties and curing kinetic of diglycidyl ether of bisphenol A cured with a phosphorus-containing diamine. J. Appl. Polym. Sci. 1999, 74 (7), 1635−1645. (43) Wang, Q.; Shi, W. Kinetics study of thermal decomposition of epoxy resins containing flame retardant components. Polym. Degrad. Stab. 2006, 91 (8), 1747−1754. (44) Qian, L.; Qiu, Y.; Sun, N.; Xu, M.; Xu, G.; Xin, F.; Chen, Y. Pyrolysis route of a novel flame retardant constructed by phosphaphenanthrene and triazine-trione groups and its flameretardant effect on epoxy resin. Polym. Degrad. Stab. 2014, 107, 98− 105. (45) Wang, Y.; Zhao, J.; Yuan, Y.; Liu, S.; Feng, Z.; Zhao, Y. Synthesis of maleimido-substituted aromatic s-triazine and its application in flame-retarded epoxy resins. Polym. Degrad. Stab. 2014, 99, 27−34. (46) Wang, X.; Song, L.; Xing, W.; Lu, H.; Hu, Y. A effective flame retardant for epoxy resins based on poly(DOPO substituted dihydroxyl phenyl pentaerythritol diphosphonate. Mater. Chem. Phys. 2011, 125 (3), 536−541. (47) Xu, W.; Wirasaputra, A.; Liu, S.; Yuan, Y.; Zhao, J. Highly effective flame retarded epoxy resin cured by DOPO-based co-curing agent. Polym. Degrad. Stab. 2015, 122, 44−51. (48) Wang, X.; Hu, Y.; Song, L.; Xing, W.; Lu, H. Thermal degradation mechanism of flame retarded epoxy resins with a DOPOsubstitued organophosphorus oligomer by TG-FTIR and DP-MS. J. Anal. Appl. Pyrolysis 2011, 92 (1), 164−170. (49) Ma, S.; Webster, D. C. Naturally Occurring Acids as CrossLinkers To Yield VOC-Free, High-Performance, Fully Bio-Based, Degradable Thermosets. Macromolecules 2015, 48 (19), 7127−7137. (50) Ma, S.; Webster, D. C.; Jabeen, F. Hard and Flexible, Degradable Thermosets from Renewable Bioresources with the Assistance of Water and Ethanol. Macromolecules 2016, 49 (10), 3780−3788. (51) Xie, T.; Rousseau, I. A. Facile tailoring of thermal transition temperatures of epoxy shape memory polymers. Polymer 2009, 50 (8), 1852−1856. (52) Liu, H.; Xu, K.; Cai, H.; Su, J.; Liu, X.; Fu, Z.; Chen, M. Thermal properties and flame retardancy of novel epoxy based on phosphorusmodified Schiff-base. Polym. Adv. Technol. 2012, 23 (1), 114−121. (53) Chen, Z.-K.; Yang, G.; Yang, J.-P.; Fu, S.-Y.; Ye, L.; Huang, Y.-G. Simultaneously increasing cryogenic strength, ductility and impact resistance of epoxy resins modified by n-butyl glycidyl ether. Polymer 2009, 50 (5), 1316−1323. Macromolecules Article DOI: 10.1021/acs.macromol.7b00097 Macromolecules 2017, 50, 1892−1901 1901
按次数下载不扣除下载券;
注册用户24小时内重复下载只扣除一次;
顺序:VIP每日次数-->可用次数-->下载券;
- 高等学校试用教材:《物理光学》书籍教材PDF电子版(共八章,浙江大学:梁铨廷).pdf
- 湖南人文科技学院:信息学院物理学专业《数学物理方法》理论课程教学大纲.doc
- 湖南人文科技学院:信息学院物理学专业《C语言程序设计》实验课程教学大纲.doc
- 湖南人文科技学院:信息学院物理学专业《物理与艺术》理论课程教学大纲.doc
- 湖南人文科技学院:信息学院物理学专业《中学物理实验教学研究》实践课程教学大纲.doc
- 湖南人文科技学院:信息学院物理学专业《物理文化与教育》理论课程教学大纲.doc
- 湖南人文科技学院:信息学院物理学专业《物理学前沿》理论课程教学大纲.doc
- 湖南人文科技学院:信息学院物理学专业《固体物理》理论课程教学大纲.doc
- 湖南人文科技学院:信息学院物理学专业《诺贝尔奖100年》理论课程教学大纲.doc
- 湖南人文科技学院:信息学院物理学专业《教育与知识能力》理论课程教学大纲.doc
- 湖南人文科技学院:信息学院物理学专业《教师职业技能训练》课程教学大纲(二)面试.doc
- 湖南人文科技学院:信息学院物理学专业《教师职业技能训练》理论课程教学大纲(一)现代教育技术.doc
- 湖南人文科技学院:信息学院物理学专业《中学教师综合素质》理论课程教学大纲.doc
- 湖南人文科技学院:信息学院物理学专业《中学物理教学论》理论课程教学大纲.doc
- 湖南人文科技学院:信息学院物理学专业《电路与电子技术》实验课程教学大纲.doc
- 湖南人文科技学院:信息学院物理学专业《近代物理实验》实验课程教学大纲.doc
- 湖南人文科技学院:信息学院物理学专业《基础物理》实验课程教学大纲(二).doc
- 湖南人文科技学院:信息学院物理学专业《基础物理》实验课程教学大纲(一).doc
- 湖南人文科技学院:信息学院物理学专业《电路与电子技术》理论课程教学大纲.doc
- 湖南人文科技学院:信息学院物理学专业《专业英语》理论课程教学大纲.doc
- 广东工业大学:《高分子物理》课程教学资源(课件讲稿)第一章 高分子链的结构.pdf
- 广东工业大学:《高分子物理》课程教学资源(英文词汇)第一章 高分子链的结构.docx
- 广东工业大学:《高分子物理》课程教学资源(课件讲稿)第二章 高分子的凝聚态结构.pdf
- 广东工业大学:《高分子物理》课程教学资源(英文词汇)第二章 高分子的聚集态结构.docx
- Chapter 06 橡胶弹性 Rubber Elasticity.pptx
- 广东工业大学:《高分子物理》课程教学资源(英文词汇)第三章 高分子溶液、第四章 聚合物的分子量和分子量分布.pdf
- 广东工业大学:《高分子物理》课程教学资源(课件讲稿)第三章 高分子溶液.pdf
- 广东工业大学:《高分子物理》课程教学资源(课件讲稿)第五章 聚合物的分子运动和转变.pdf
- 广东工业大学:《高分子物理》课程教学资源(英文词汇)第五章 聚合物的转变与松弛.docx
- 广东工业大学:《高分子物理》课程教学资源(英文词汇)第六章 橡胶弹性.docx
- 广东工业大学:《高分子物理》课程教学资源(课件讲稿)第六章 橡胶弹性.pdf
- 《高分子物理》课程教学资源(文献资料)橡胶弹性——Chemie in nserer Zeit - 2009 - Kloppenburg - Das elastische Jahrhundert Synthesekautschuke.pdf
- 《高分子物理》课程教学资源(文献资料)橡胶弹性——Tube Models for Rubber-Elastic Systems.pdf
- 广东工业大学:《高分子物理》课程教学资源(课件讲稿)第四章 聚合物的分子量和分子量分布(打印版).pdf
- 广东工业大学:《高分子物理》课程教学资源(课件讲稿)第七章 聚合物的粘弹性 Polymer Viscoelasticity(打印版).pdf
- 广东工业大学:《高分子物理》课程教学资源(英文词汇)第七章 聚合物的粘弹性.docx
- 广东工业大学:《高分子物理》课程教学资源(课件讲稿)第九章 聚合物的流变性 Polymer Rheology.pdf
- 广东工业大学:《高分子物理》课程教学资源(课件讲稿)第八章 聚合物的力学性能 Mechanical Properties of Polymers(打印版).pdf
- 广东工业大学:《高分子物理》课程教学资源(英文词汇)第八章 聚合物的屈服和断裂.docx
- 广东工业大学:《高分子物理》课程教学资源(课件讲稿)第十章 聚合物的电学性能、热学性能和光学性能.pdf