《纺织复合材料》课程参考文献(Mechanics of Composite Materials)06 Bending of Beams

Bending of Beams Chapter Objectives Develop formulas to find the deflection and stresses in a beam made of composite materials. Develop formulas for symmetric beams that are narrow or wide. Develop formulas for nonsymmetric beams that are narrow or wide. 6.1 Introduction To study mechanics of beams made of laminated composite materials,we need to review the beam analysis of isotropic materials.Several concepts applied to beams made of isotropic materials will help in understanding beams made of composite materials.We are limiting our study to beams with transverse loading or applied moments. The bending stress in an isotropic beam(Figure 6.1 and Figure 6.2)under an applied bending moment,M,is given by 2 (6.1) where z=distance from the centroid I=second moment of area The bending deflections,w,are given by solving the differential equation 431 2006 by Taylor Francis Group,LLC
431 6 Bending of Beams Chapter Objectives • Develop formulas to find the deflection and stresses in a beam made of composite materials. • Develop formulas for symmetric beams that are narrow or wide. • Develop formulas for nonsymmetric beams that are narrow or wide. 6.1 Introduction To study mechanics of beams made of laminated composite materials, we need to review the beam analysis of isotropic materials. Several concepts applied to beams made of isotropic materials will help in understanding beams made of composite materials. We are limiting our study to beams with transverse loading or applied moments. The bending stress in an isotropic beam (Figure 6.1 and Figure 6.2) under an applied bending moment, M, is given by1,2 , (6.1) where z = distance from the centroid I = second moment of area The bending deflections, w, are given by solving the differential equation σ = Mz I 1343_book.fm Page 431 Tuesday, September 27, 2005 11:53 AM © 2006 by Taylor & Francis Group, LLC
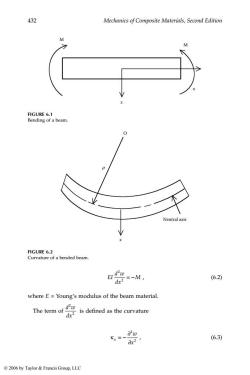
432 Mechanics of Composite Materials,Second Edition M M FIGURE 6.1 Bending of a beam. Neutral axis FIGURE 6.2 Curvature of a bended beam. EI dw dr? =-M, (6.2) where E=Young's modulus of the beam material. d-w The term of dx2 is defined as the curvature w Kx=- a2 (6.3) 2006 by Taylor Francis Group,LLC
432 Mechanics of Composite Materials, Second Edition , (6.2) where E = Young’s modulus of the beam material. The term of is defined as the curvature , (6.3) FIGURE 6.1 Bending of a beam. FIGURE 6.2 Curvature of a bended beam. M M z x O z Neutral axis ρ EI d w dx M 2 2 = − d w dx 2 2 κx w x = − ∂ ∂ 2 2 1343_book.fm Page 432 Tuesday, September 27, 2005 11:53 AM © 2006 by Taylor & Francis Group, LLC
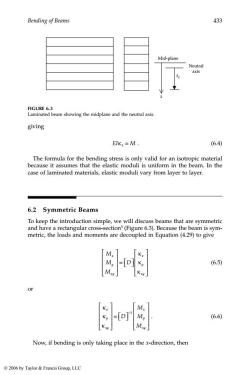
Bending of Beams 433 Mid-plane Neutral axis FIGURE 6.3 Laminated beam showing the midplane and the neutral axis. giving EIK:=M. (6.4) The formula for the bending stress is only valid for an isotropic material because it assumes that the elastic moduli is uniform in the beam.In the case of laminated materials,elastic moduli vary from layer to layer. 6.2 Symmetric Beams To keep the introduction simple,we will discuss beams that are symmetric and have a rectangular cross-section3(Figure 6.3).Because the beam is sym- metric,the loads and moments are decoupled in Equation(4.29)to give Kx D (6.5) or Kx M Ky =[D My (6.6) Now,if bending is only taking place in the x-direction,then 2006 by Taylor Francis Group,LLC
Bending of Beams 433 giving . (6.4) The formula for the bending stress is only valid for an isotropic material because it assumes that the elastic moduli is uniform in the beam. In the case of laminated materials, elastic moduli vary from layer to layer. 6.2 Symmetric Beams To keep the introduction simple, we will discuss beams that are symmetric and have a rectangular cross-section3 (Figure 6.3). Because the beam is symmetric, the loads and moments are decoupled in Equation (4.29) to give (6.5) or . (6.6) Now, if bending is only taking place in the x-direction, then FIGURE 6.3 Laminated beam showing the midplane and the neutral axis. zc Mid-plane z Neutral axis EIκ =x M M M M D x y xy x y xy ⎡ ⎣ ⎢ ⎢ ⎢ ⎤ ⎦ ⎥ ⎥ ⎥ = ⎡ ⎣ ⎤ ⎦ ⎡ ⎣ ⎢ ⎢ ⎢ ⎤ ⎦ ⎥ ⎥ ⎥ κ κ κ κ κ κ x y xy x y xy D M M M ⎡ ⎣ ⎢ ⎢ ⎢ ⎤ ⎦ ⎥ ⎥ ⎥ = ⎡ ⎣ ⎤ ⎦ ⎡ ⎣ ⎢ ⎢ ⎢ ⎤ ⎦ ⎥ ⎥ ⎥ −1 1343_book.fm Page 433 Tuesday, September 27, 2005 11:53 AM © 2006 by Taylor & Francis Group, LLC
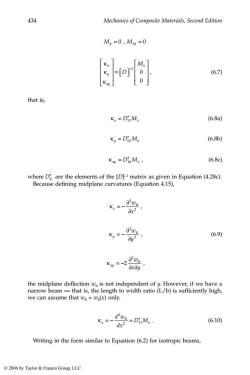
434 Mechanics of Composite Materials,Second Edition My =0,Mxy=0 M: = (6.7) 0 that is, K=DiM (6.8a) Ky=Di2M (6.8b) Kw DieM:, (6.8c) where D are the elements of the [D]-1 matrix as given in Equation(4.28c) Because defining midplane curvatures(Equation 4.15), K=-02 dx2 wo Ky=- (6.9) Ky=-2 子wa dxdy the midplane deflection wo is not independent of y.However,if we have a narrow beam-that is,the length to width ratio (L/b)is sufficiently high, we can assume that wo=wo(x)only. K=-=DiM,. (6.10) dx2 Writing in the form similar to Equation(6.2)for isotropic beams, 2006 by Taylor Francis Group,LLC
434 Mechanics of Composite Materials, Second Edition , , (6.7) that is, (6.8a) (6.8b) , (6.8c) where are the elements of the [D]–1 matrix as given in Equation (4.28c). Because defining midplane curvatures (Equation 4.15), , , (6.9) , the midplane deflection w0 is not independent of y. However, if we have a narrow beam — that is, the length to width ratio (L/b) is sufficiently high, we can assume that w0 = w0(x) only. . (6.10) Writing in the form similar to Equation (6.2) for isotropic beams, My = 0 Mxy = 0 κ κ κ x y xy x D ⎡ M ⎣ ⎢ ⎢ ⎢ ⎤ ⎦ ⎥ ⎥ ⎥ = ⎡ ⎣ ⎤ ⎦ ⎡ ⎣ ⎢ ⎢ ⎢ ⎤ ⎦ ⎥ ⎥ ⎥ −1 0 0 κx x = D M∗ 11 κy x = D M∗ 12 κxy = D Mx ∗ 16 Dij ∗ κx w x = − ∂ ∂ 2 0 2 κy w y = − ∂ ∂ 2 0 2 κxy w x y = − ∂ ∂ ∂ 2 2 0 κx x d w dx = − = D M∗ 2 0 2 11 1343_book.fm Page 434 Tuesday, September 27, 2005 11:53 AM © 2006 by Taylor & Francis Group, LLC
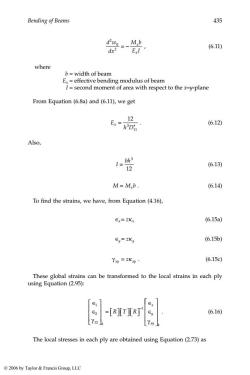
Bending of Beams 435 Mb dx2 E,I' (6.11) where b=width of beam Ex=effective bending modulus of beam I=second moment of area with respect to the x-y-plane From Equation(6.8a)and (6.11),we get 12 Ex=HDi (6.12) Also, 1奶3 (6.13) 12 M=M,b. (6.14) To find the strains,we have,from Equation (4.16), ∈x=ZKx (6.15a) ∈g=zKy (6.15b) Yy=zKw· (6.15c) These global strains can be transformed to the local strains in each ply using Equation(2.95): r (6.16) The local stresses in each ply are obtained using Equation(2.73)as 2006 by Taylor Francis Group,LLC
Bending of Beams 435 , (6.11) where b = width of beam Ex = effective bending modulus of beam I = second moment of area with respect to the x–y-plane From Equation (6.8a) and (6.11), we get . (6.12) Also, (6.13) . (6.14) To find the strains, we have, from Equation (4.16), (6.15a) (6.15b) . (6.15c) These global strains can be transformed to the local strains in each ply using Equation (2.95): . (6.16) The local stresses in each ply are obtained using Equation (2.73) as d w dx M b E I x x 2 0 2 = − E h D x = ∗ 12 3 11 I bh = 3 12 M M= xb ∈ =x x zκ ∈ =y y zκ γ κ xy xy = z ∈ ∈ ⎡ ⎣ ⎢ ⎢ ⎢ ⎤ ⎦ ⎥ ⎥ ⎥ = ⎡ ⎣ ⎤ ⎦⎡ ⎣ ⎤ ⎦⎡ ⎣ ⎤ ⎦ ∈ ∈ − 1 2 12 1 γ γ k x y xy R T R ⎡ ⎣ ⎢ ⎢ ⎢ ⎤ ⎦ ⎥ ⎥ ⎥ k 1343_book.fm Page 435 Tuesday, September 27, 2005 11:53 AM © 2006 by Taylor & Francis Group, LLC

436 Mechanics of Composite Materials,Second Edition =[ (6.17) Y12 The global stresses in each ply are then obtained using Equation(2.89)as 61 =[r (6.18) Example 6.1 A simply supported laminated composite beam of length 0.1 m and width 5 mm(Figure 6.4)made of graphite/epoxy has the following layup of [0/ 90/-30/30].A uniform load of 200 N/m is applied on the beam.What is the maximum deflection of the beam?Find the local stresses at the top of the third ply(-30)from the top.Assume that each ply is 0.125 mm thick and the properties of unidirectional graphite/epoxy are as given in Table 2.1. Solution The shear and bending moment diagrams for the beam are given in Figure 6.5.The bending moment is maximum at the center of the beam and is given by M92 8 (6.19) where g=load intensity (N/m) L=length of the beam(m) q=200N/m 77 0.1m >5mm FIGURE 6.4 Uniformly loaded simply supported beam. 2006 by Taylor Francis Group,LLC
436 Mechanics of Composite Materials, Second Edition . (6.17) The global stresses in each ply are then obtained using Equation (2.89) as . (6.18) Example 6.1 A simply supported laminated composite beam of length 0.1 m and width 5 mm (Figure 6.4) made of graphite/epoxy has the following layup of [0/ 90/–30/30]s. A uniform load of 200 N/m is applied on the beam. What is the maximum deflection of the beam? Find the local stresses at the top of the third ply (–30°) from the top. Assume that each ply is 0.125 mm thick and the properties of unidirectional graphite/epoxy are as given in Table 2.1. Solution The shear and bending moment diagrams for the beam are given in Figure 6.5. The bending moment is maximum at the center of the beam and is given by , (6.19) where q = load intensity (N/m) L = length of the beam (m) FIGURE 6.4 Uniformly loaded simply supported beam. σ σ τ γ 1 2 12 1 2 12 ⎡ ⎣ ⎢ ⎢ ⎢ ⎤ ⎦ ⎥ ⎥ ⎥ = ⎡ ⎣ ⎤ ⎦ ∈ ∈ ⎡ ⎣ ⎢ ⎢ ⎢ ⎤ ⎦ ⎥ ⎥ ⎥ k k Q σ σ τ σ σ τ x y xy k T ⎡ ⎣ ⎢ ⎢ ⎢ ⎤ ⎦ ⎥ ⎥ ⎥ = ⎡ ⎣ ⎤ ⎦ ⎡ ⎣ ⎢ ⎢ ⎢ ⎤ ⎦ ⎥ ⎥ ⎥ −1 1 2 12 k M qL = 2 8 5 mm q = 200 N/m 0.1 m 1343_book.fm Page 436 Tuesday, September 27, 2005 11:53 AM © 2006 by Taylor & Francis Group, LLC
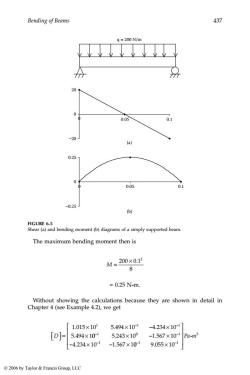
Bending of Beams 437 q=200N/m 20 0.05 0.1 -20 (a) 0.25 0 0.05 0.1 -0.25J (b) FIGURE 6.5 Shear(a)and bending moment(b)diagrams of a simply supported beam. The maximum bending moment then is M=200×0.12 8 =0.25N-m. Without showing the calculations because they are shown in detail in Chapter 4(see Example 4.2),we get 1.015×10 5.494×10 -4.234×10-1 [D]- 5.494×101 5.243×10° -1.567×10- Pa-m3 -4.234×10-1 -1.567×10-1 9.055×101 2006 by Taylor Francis Group,LLC
Bending of Beams 437 The maximum bending moment then is = 0.25 N-m. Without showing the calculations because they are shown in detail in Chapter 4 (see Example 4.2), we get FIGURE 6.5 Shear (a) and bending moment (b) diagrams of a simply supported beam. q = 200 N/m (b) (a) 0 0 20 −20 0.05 0.1 0.25 0 0 0.05 0.1 −0.25 M = 200 × 0 1 8 2 . ⎡ ⎣D⎤ ⎦ = × × − × × − − 1 015 10 5 494 10 4 234 10 5 494 1 1 1 1 . . . . 0 5 243 10 1 567 10 4 234 10 1 567 1 1 0 1 1 − − − × − × − × − × . . . . 0 9 055 10 1 1 3 − − × ⎡ ⎣ ⎢ ⎢ ⎢ ⎤ ⎦ ⎥ ⎥ ⎥ . Pa-m 1343_book.fm Page 437 Tuesday, September 27, 2005 11:53 AM © 2006 by Taylor & Francis Group, LLC

438 Mechanics of Composite Materials,Second Edition 1.009×10 -9.209×10-3 4.557×10-21 [D' -9.209×10-3 1.926×10-1 2.901×10-2 4.557×102 2.901×10-2 1.131×10° Pa-m3 To find the maximum deflection of the beam,6,we use the isotropic beam formula: 6-5qL (6.20) 384E,I Now,in Equation(6.12), h=(8)0.125×10) =0.001m D1=1.009×10-11 Pa-m3 Thus, 12 ExDi 12 (0.0011.009×10 =1.189×101Pa From Equation(6.13), 13 12 _(5×103)0.001)月 12 =4.167×10-13m4 2006 by Taylor Francis Group,LLC
438 Mechanics of Composite Materials, Second Edition . To find the maximum deflection of the beam, δ, we use the isotropic beam formula: . (6.20) Now, in Equation (6.12), . Thus, From Equation (6.13), ⎡ ⎣D⎤ ⎦ = × − × × − − − − 1 1 3 2 1 009 10 9 209 10 4 557 10 9 20 . . . . 9 10 1 926 10 2 901 10 4 557 10 2 901 3 1 2 2 × × × × × − − − − . . . . 10 1 131 10 1 2 0 3 − × ⎡ ⎣ ⎢ ⎢ ⎢ ⎤ ⎦ ⎥ ⎥ ⎥ . Pa-m δ = 5 384 4 qL E Ix h = ( )( ) × − 8 0 125 10 3 . = 0.001m D Pa m 11 1 3 1 009 10 ∗ − 1 = × − . E h D x = = ( ) ( ) × = × ∗ − 12 12 0 001 1 009 10 1 189 10 3 11 3 1 . . . 11Pa I bh m = = ( ) × ( ) = × − − 3 3 3 13 4 12 5 10 0 001 12 4 167 10 . . . 1343_book.fm Page 438 Tuesday, September 27, 2005 11:53 AM © 2006 by Taylor & Francis Group, LLC

Bending of Beams 439 Therefore,from Equation (6.20), 6= (⑤)(200)(0.1° (3841.189×104.167×10-8 =5.256×10-3m =5.256171m. The maximum curvature is at the middle of the beam and is given by Di Di2 9L2 Xy 8b Die 1.009×101 -9.209×10-3 200×0.12 4.557×10-2 8×0.005 1.009×10-11 -9.209×10-3 50 4.557×10-2 5.045 1 -0.4605 m 2.279 The global strains(Equation 6.15)at the top of the third ply(-30)are Ex Kx ∈y =Z Yw] 5.045 =(-0.00025 -0.4605 2.279 2006 by Taylor Francis Group,LLC
Bending of Beams 439 Therefore, from Equation (6.20), . The maximum curvature is at the middle of the beam and is given by . The global strains (Equation 6.15) at the top of the third ply (–30°) are δ = ( )( )( ) ( )( ) × × − 5 200 0 1 384 1 189 10 4 167 10 4 11 1 . . . 3 ( ) = × − 5 256 10 3 . m = 5.256 mm χ χ χ x y xy D D D qL ⎡ ⎣ ⎢ ⎢ ⎢ ⎤ ⎦ ⎥ ⎥ ⎥ = ⎡ ⎣ ⎢ ⎢ ⎢ ⎤ ⎦ ⎥ ⎥ ⎥ ∗ ∗ ∗ 11 12 16 2 8b = × − × × ⎡ ⎣ ⎢ ⎢ ⎢ ⎤ ⎦ ⎥ ⎥ ⎥ − − − 1 009 10 9 209 10 4 557 10 2 1 3 2 . . . 00 0 1 8 0 005 2 × × . . = × − × × ⎡ ⎣ ⎢ ⎢ ⎢ ⎤ ⎦ ⎥ ⎥ ⎥ − − − 1 009 10 9 209 10 4 557 10 5 1 3 2 . . . 0 = − ⎡ ⎣ ⎢ ⎢ ⎢ ⎤ ⎦ ⎥ ⎥ ⎥ 5 045 0 4605 2 279 1 . . . m ∈ ∈ ⎡ ⎣ ⎢ ⎢ ⎢ ⎤ ⎦ ⎥ ⎥ ⎥ = ⎡ ⎣ ⎢ ⎢ ⎢ ⎤ ⎦ ⎥ ⎥ ⎥ x y xy x y xy z γ κ κ κ = −( ) − ⎡ ⎣ ⎢ ⎢ ⎢ ⎤ ⎦ ⎥ ⎥ ⎥ 0 00025 5 045 0 4605 2 279 . . . . 1343_book.fm Page 439 Tuesday, September 27, 2005 11:53 AM © 2006 by Taylor & Francis Group, LLC
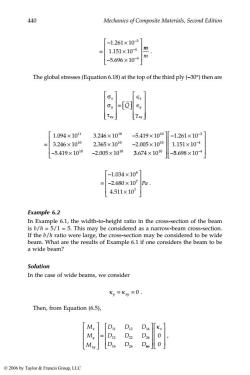
440 Mechanics of Composite Materials,Second Edition -1.261×10-31 1.151×10+ m m -5.696×10 The global stresses(Equation 6.18)at the top of the third ply(-30)then are 刘】 Yy」 1.094×101 3.246×1010 -5.419×1010] -1.261×10-3 3.246×1010 2.365×1010 -2.005×1010 1.151×10 -5.419×100 -2.005×1010 3.674×1010 -5.698×104 -1.034×108 -2.680×107 Pa. 4.511×107 Example 6.2 In Example 6.1,the width-to-height ratio in the cross-section of the beam is b/h=5/1 =5.This may be considered as a narrow-beam cross-section. If the b/h ratio were large,the cross-section may be considered to be wide beam.What are the results of Example 6.1 if one considers the beam to be a wide beam? Solution In the case of wide beams,we consider Ky=Kxy=0. Then,from Equation (6.5), M (Du D12 D16 My D12 D22 0 D16 D26 Do 0 2006 by Taylor Francis Group,LLC
440 Mechanics of Composite Materials, Second Edition . The global stresses (Equation 6.18) at the top of the third ply (–30°) then are . Example 6.2 In Example 6.1, the width-to-height ratio in the cross-section of the beam is b/h = 5/1 = 5. This may be considered as a narrow-beam cross-section. If the b/h ratio were large, the cross-section may be considered to be wide beam. What are the results of Example 6.1 if one considers the beam to be a wide beam? Solution In the case of wide beams, we consider . Then, from Equation (6.5), , = − × × − × ⎡ ⎣ ⎢ ⎢ ⎢ ⎤ ⎦ ⎥ ⎥ ⎥ − − − 1 261 10 1 151 10 5 696 10 3 4 4 . . . m m σ σ τ γ x y xy x y xy Q ⎡ ⎣ ⎢ ⎢ ⎢ ⎢ ⎤ ⎦ ⎥ ⎥ ⎥ ⎥ = ⎡ ⎣ ⎤ ⎦ ∈ ∈ ⎡ ⎣ ⎢ ⎢ ⎢ ⎢ ⎤ ⎦ ⎥ ⎥ ⎥ ⎥ = × × − × × 1 094 10 3 246 10 5 419 10 3 246 10 2 11 10 10 10 . . . . . . . . 365 10 2 005 10 5 419 10 2 005 10 10 10 10 10 × − × − × − × 3 674 10 1 261 10 1 151 10 10 3 4 . . . × ⎡ ⎣ ⎢ ⎢ ⎢ ⎤ ⎦ ⎥ ⎥ ⎥ − × × − − − 5 698 10 4 . × ⎡ ⎣ ⎢ ⎢ ⎢ ⎤ ⎦ ⎥ ⎥ − ⎥ = − × − × × ⎡ ⎣ ⎢ ⎢ ⎢ ⎤ ⎦ ⎥ ⎥ ⎥ 1 034 10 2 680 10 4 511 10 8 7 7 . . . Pa κ κ y x = = y 0 M M M D D D DDD DDD x y xy ⎡ ⎣ ⎢ ⎢ ⎢ ⎤ ⎦ ⎥ ⎥ ⎥ = 11 12 16 12 22 26 16 26 66 0 0 ⎡ ⎣ ⎢ ⎢ ⎢ ⎤ ⎦ ⎥ ⎥ ⎥ ⎡ ⎣ ⎢ ⎢ ⎢ ⎤ ⎦ ⎥ ⎥ ⎥ κx 1343_book.fm Page 440 Tuesday, September 27, 2005 11:53 AM © 2006 by Taylor & Francis Group, LLC
按次数下载不扣除下载券;
注册用户24小时内重复下载只扣除一次;
顺序:VIP每日次数-->可用次数-->下载券;
- 《纺织复合材料》课程参考文献(Mechanics of Composite Materials)05 Failure, Analysis, and Design of Laminates.pdf
- 《纺织复合材料》课程参考文献(Mechanics of Composite Materials)03 Micromechanical Analysis of a Lamina.pdf
- 《纺织复合材料》课程参考文献(Mechanics of Composite Materials)02 Macromechanical Analysis of a Lamina.pdf
- 《纺织复合材料》课程参考文献(Mechanics of Composite Materials)01 Introduction to Composite Materials.pdf
- 《纺织复合材料》课程参考文献(High Performance Thermoplastic Resins and Their Composites)Contents and Subject Index.pdf
- 《纺织复合材料》课程参考文献(High Performance Thermoplastic Resins and Their Composites)Foreword.pdf
- 《纺织复合材料》课程参考文献(High Performance Thermoplastic Resins and Their Composites)09. References.pdf
- 《纺织复合材料》课程参考文献(High Performance Thermoplastic Resins and Their Composites)08. Summary, Conclusions and Recommendations.pdf
- 《纺织复合材料》课程参考文献(High Performance Thermoplastic Resins and Their Composites)07. Costs and Aircraft Applications of Thermoplastic Composites.pdf
- 《纺织复合材料》课程参考文献(High Performance Thermoplastic Resins and Their Composites)06. Joining Thermoplastic Composites.pdf
- 《纺织复合材料》课程参考文献(High Performance Thermoplastic Resins and Their Composites)05. Processing of Advanced Thermoplastic Composites.pdf
- 《纺织复合材料》课程参考文献(High Performance Thermoplastic Resins and Their Composites)03. Morphology.pdf
- 《纺织复合材料》课程参考文献(High Performance Thermoplastic Resins and Their Composites)02. Neat Thermoplastic Resins Properties.pdf
- 《纺织复合材料》课程参考文献(High Performance Thermoplastic Resins and Their Composites)01. Introduction.pdf
- 《纺织复合材料》课程参考文献(Fibers and Composites)CONTENTS.pdf
- 《纺织复合材料》课程参考文献(Fibers and Composites)10 CARBON–CEMENT COMPOSITES.pdf
- 《纺织复合材料》课程参考文献(Fibers and Composites)08 STRUCTURE OF PYROCARBONS.pdf
- 《纺织复合材料》课程参考文献(Fibers and Composites)07 LIQUID IMPREGNATION TECHNIQUES FOR CARBON–CARBON COMPOSITES.pdf
- 《纺织复合材料》课程参考文献(Fibers and Composites)06 INDUSTRIAL CARBON CHEMICAL VAPOR INFILTRATION(CVI)PROCESSES.pdf
- 《纺织复合材料》课程参考文献(Fibers and Composites)05 CHEMICAL VAPOR INFILTRATION PROCESSES OF CARBON MATERIALS.pdf
- 《纺织复合材料》课程参考文献(Mechanics of Composite Materials with MATLAB)00 Contents.pdf
- 《纺织复合材料》课程参考文献(Mechanics of Composite Materials with MATLAB)01 Introduction.pdf
- 《纺织复合材料》课程参考文献(Mechanics of Composite Materials with MATLAB)02 Linear Elastic Stress-Strain Relations.pdf
- 《纺织复合材料》课程参考文献(Mechanics of Composite Materials with MATLAB)03 Elastic Constants Based on Micromechanics.pdf
- 《纺织复合材料》课程参考文献(Mechanics of Composite Materials with MATLAB)04 Plane Stress.pdf
- 《纺织复合材料》课程参考文献(Mechanics of Composite Materials with MATLAB)05 Global Coordinate System.pdf
- 《纺织复合材料》课程参考文献(Mechanics of Composite Materials with MATLAB)06 Elastic Constants Based on Global Coordinate System.pdf
- 《纺织复合材料》课程参考文献(Mechanics of Composite Materials with MATLAB)07 Laminate Analysis – Part I.pdf
- 《纺织复合材料》课程参考文献(Mechanics of Composite Materials with MATLAB)08 Laminate Analysis – Part II.pdf
- 《纺织复合材料》课程参考文献(Mechanics of Composite Materials with MATLAB)09 Effective Elastic Constants of a Laminate.pdf
- 《纺织复合材料》课程参考文献(Mechanics of Composite Materials with MATLAB)10 Failure Theories of a Lamina.pdf
- 《纺织复合材料》课程参考文献(Mechanics of Composite Materials with MATLAB)11 Introduction to Homogenization of Composite Materials.pdf
- 《纺织复合材料》课程参考文献(Mechanics of Composite Materials with MATLAB)12 Introduction to Damage Mechanics of Composite Materials.pdf
- 《纺织复合材料》课程参考文献(Mechanics of Composite Materials with MATLAB)13 Solutions to Problems.pdf
- 《纺织复合材料》课程参考文献(Mechanics of Composite Structures)01 Introduction.pdf
- 《纺织复合材料》课程参考文献(Mechanics of Composite Structures)02 Displacements, Strains, and Stresses.pdf
- 《纺织复合材料》课程参考文献(Mechanics of Composite Structures)03 Laminated Composites.pdf
- 《纺织复合材料》课程参考文献(Mechanics of Composite Structures)04 Thin Plates.pdf
- 《纺织复合材料》课程参考文献(Mechanics of Composite Structures)05 Sandwich Plates.pdf
- 《纺织复合材料》课程参考文献(Mechanics of Composite Structures)06 Beams.pdf