《纺织复合材料》课程参考文献(Experimental Characterization of Advanced Composite Materials, Third Edition)12 Laminate Thermoelastic Response

12 Laminate Thermoelastic Response The thermoelastic response of a general laminate may be very complex [1].For the particular case of unsymmetric laminates,bending-extension coupling, Equations (2.44)and (2.45)indicate the existence of out-of-plane deflections for a laminate subject to a temperature change.Hyer [2]and Dang and Hyer [3]have performed very detailed experiments and analysis of warping defor- mations of unsymmetric composite laminates during cooling from elevated (cure)temperatures.For symmetric laminates,however,it can be shown that the bending-extension coupling disappears,[B]=[0].For a balanced laminate,A=A26=0.Hence,a symmetric and balanced laminate behaves as a homogeneous orthotropic material in a macroscopic sense.Typical balanced symmetric laminates are [0/+45/90],[02/+45]3,and [02/902ls. For a symmetric and balanced laminate,Equation(2.51)yields 日& (12.1) where [NT]and [MT]are given by Equations (2.37)and(2.38).It may also be shown that the thermal moment resultants vanish,[MT]=[0],and the thermal in-plane shear force resultant N=0.Equations(12.1)then yield [e]=[A']N鬥 (12.2a) [K=[O (12.2b) Hence,a symmetric laminate does not bend due to a temperature change (Equation(12.2b)).The expanded form of Equation (12.2a)is N (12.3) 0 Consequently,Ysy=0,which shows that a balanced laminate will not deform in shear due to the temperature change. ©2003 by CRC Press LLC
12 Laminate Thermoelastic Response The thermoelastic response of a general laminate may be very complex [1]. For the particular case of unsymmetric laminates, bending–extension coupling, Equations (2.44) and (2.45) indicate the existence of out-of-plane deflections for a laminate subject to a temperature change. Hyer [2] and Dang and Hyer [3] have performed very detailed experiments and analysis of warping deformations of unsymmetric composite laminates during cooling from elevated (cure) temperatures. For symmetric laminates, however, it can be shown that the bending–extension coupling disappears, [B] = [0]. For a balanced laminate, A16 = A26 = 0. Hence, a symmetric and balanced laminate behaves as a homogeneous orthotropic material in a macroscopic sense. Typical balanced symmetric laminates are [0/±45/90]s, [02/±45]s, and [02/902]s. For a symmetric and balanced laminate, Equation (2.51) yields (12.1) where [NT] and [MT] are given by Equations (2.37) and (2.38). It may also be shown that the thermal moment resultants vanish, [MT] = [0], and the thermal in-plane shear force resultant = 0. Equations (12.1) then yield (12.2a) [κ] = [0] (12.2b) Hence, a symmetric laminate does not bend due to a temperature change (Equation (12.2b)). The expanded form of Equation (12.2a) is (12.3) Consequently, γxy = 0, which shows that a balanced laminate will not deform in shear due to the temperature change. ε κ o = ′ ′ = A D N M T T 0 0 Nxy T ε0 [ ] = [ ] A N ′ [ ] T ε ε γ x y xy x T y T A A A A A N N = ′ ′ ′ ′ ′ 11 12 12 22 66 0 0 00 0 TX001_ch12_Frame Page 163 Saturday, September 21, 2002 5:05 AM © 2003 by CRC Press LLC
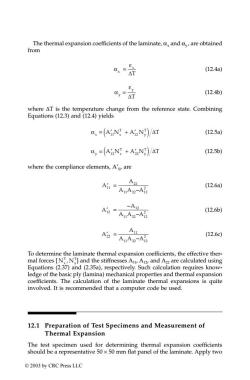
The thermal expansion coefficients of the laminate,and d,are obtained from 0x= Ex (12.4a) △T dy=AT (12.4b) where AT is the temperature change from the reference state.Combining Equations (12.3)and (12.4)yields =(AiN:+AiNy)/AT (12.5a) y=(AiNT +ANT)/AT (12.5b) where the compliance elements,Air are Ai =AuA2-A品 (12.6a) -A12 An =AuAz-Ais (12.6b) A A2-AuA-Ai (12.6c) To determine the laminate thermal expansion coefficients,the effective ther- mal forces [NT,NT]and the stiffnesses An,A,and Az are calculated using Equations (2.37)and (2.35a),respectively.Such calculation requires know- ledge of the basic ply (lamina)mechanical properties and thermal expansion coefficients.The calculation of the laminate thermal expansions is quite involved.It is recommended that a computer code be used. 12.1 Preparation of Test Specimens and Measurement of Thermal Expansion The test specimen used for determining thermal expansion coefficients should be a representative 50 x 50 mm flat panel of the laminate.Apply two ©2003 by CRC Press LLC
The thermal expansion coefficients of the laminate, αx and αy, are obtained from (12.4a) (12.4b) where ∆T is the temperature change from the reference state. Combining Equations (12.3) and (12.4) yields (12.5a) (12.5b) where the compliance elements, A′ij, are (12.6a) (12.6b) (12.6c) To determine the laminate thermal expansion coefficients, the effective thermal forces [ ] and the stiffnesses A11, A12, and A22 are calculated using Equations (2.37) and (2.35a), respectively. Such calculation requires knowledge of the basic ply (lamina) mechanical properties and thermal expansion coefficients. The calculation of the laminate thermal expansions is quite involved. It is recommended that a computer code be used. 12.1 Preparation of Test Specimens and Measurement of Thermal Expansion The test specimen used for determining thermal expansion coefficients should be a representative 50 × 50 mm flat panel of the laminate. Apply two α ε x x T = ∆ α ε y y T = ∆ αx x T y T = ( ) AN A N T ′ + ′ 11 12 ∆ αy x T y T = ( ) AN AN T ′ + ′ 12 22 ∆ ′ = − A A AA A 11 22 11 22 12 2 ′ = − − A A AA A 12 12 11 22 12 2 ′ = − A A AA A 22 11 11 22 12 2 N Nx T y T , TX001_ch12_Frame Page 164 Saturday, September 21, 2002 5:05 AM © 2003 by CRC Press LLC
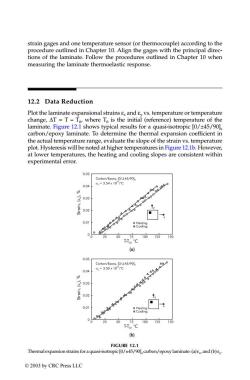
strain gages and one temperature sensor (or thermocouple)according to the procedure outlined in Chapter 10.Align the gages with the principal direc- tions of the laminate.Follow the procedures outlined in Chapter 10 when measuring the laminate thermoelastic response. 12.2 Data Reduction Plot the laminate expansional strains &x and E,vs.temperature or temperature change,AT=T-To,where To is the initial(reference)temperature of the laminate.Figure 12.1 shows typical results for a quasi-isotropic [0/+45/90 carbon/epoxy laminate.To determine the thermal expansion coefficient in the actual temperature range,evaluate the slope of the strain vs.temperature plot.Hysteresis will be noted at higher temperatures in Figure 12.1b.However, at lower temperatures,the heating and cooling slopes are consistent within experimental error. 0.05 Carbon/Epory,[0/45/901s 0.=3.54×10/℃ 0.04 alo 20.03 00 0.02 0.01 &889 0 50 75 100 125 150 T-To,C (a) 0.05 Carbon/Epoxy,[0/45/901s 0.04 a,=3.50x10rC 30.03 0.02 0.01 50 75 100 125 150 T-To,C ) FIGURE 12.1 Thermal expansion strains for a quasi-isotropic [0/45/901,carbon/epoxy laminate:(a),and(b). ©2003 by CRC Press LLC
strain gages and one temperature sensor (or thermocouple) according to the procedure outlined in Chapter 10. Align the gages with the principal directions of the laminate. Follow the procedures outlined in Chapter 10 when measuring the laminate thermoelastic response. 12.2 Data Reduction Plot the laminate expansional strains εx and εy vs. temperature or temperature change, ∆T = T – T0, where T0 is the initial (reference) temperature of the laminate. Figure 12.1 shows typical results for a quasi-isotropic [0/±45/90]s carbon/epoxy laminate. To determine the thermal expansion coefficient in the actual temperature range, evaluate the slope of the strain vs. temperature plot. Hysteresis will be noted at higher temperatures in Figure 12.1b. However, at lower temperatures, the heating and cooling slopes are consistent within experimental error. FIGURE 12.1 Thermal expansion strains for a quasi-isotropic [0/±45/90]s carbon/epoxy laminate: (a) εx, and (b) εy. TX001_ch12_Frame Page 165 Saturday, September 21, 2002 5:05 AM © 2003 by CRC Press LLC
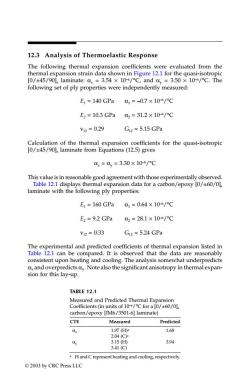
12.3 Analysis of Thermoelastic Response The following thermal expansion coefficients were evaluated from the thermal expansion strain data shown in Figure 12.1 for the quasi-isotropic [0/±45/90l,laminate::a=3.54×106/C,anda,=3.50×10-6/℃.The following set of ply properties were independently measured: E1=140GPa41=-0.7×106/C E2=10.3GPa02=31.2×106/°C V12=0.29 G2=5.15GPa Calculation of the thermal expansion coefficients for the quasi-isotropic [0/+45/90]s laminate from Equations (12.5)gives 0x=0=3.30×10/C This value is in reasonable good agreement with those experimentally observed. Table 12.1 displays thermal expansion data for a carbon/epoxy [0/+60/0]s laminate with the following ply properties: E,=160GPa%1=0.64×10-6/C E,=9.2 GPa 02=28.1×106/C V12=0.33 G12=5.24GPa The experimental and predicted coefficients of thermal expansion listed in Table 12.1 can be compared.It is observed that the data are reasonably consistent upon heating and cooling.The analysis somewhat underpredicts o and overpredicts a.Note also the significant anisotropy in thermal expan- sion for this lay-up. TABLE 12.1 Measured and Predicted Thermal Expansion Coefficients (in units of 10-/C for a [0/+60/0] carbon/epoxy [IM6/3501-6]laminate) CTE Measured Predicted 04 1.97(H) 1.68 2.04(C 04 3.15(H) 3.94 3.41(C) Hand C represent heating and cooling,respectively. ©2003 by CRC Press LLC
12.3 Analysis of Thermoelastic Response The following thermal expansion coefficients were evaluated from the thermal expansion strain data shown in Figure 12.1 for the quasi-isotropic [0/±45/90]s laminate: αx = 3.54 × 10–6/°C, and αy = 3.50 × 10–6/°C. The following set of ply properties were independently measured: E1 = 140 GPa α1 = –0.7 × 10–6/°C E2 = 10.3 GPa α2 = 31.2 × 10–6/°C ν12 = 0.29 G12 = 5.15 GPa Calculation of the thermal expansion coefficients for the quasi-isotropic [0/±45/90]s laminate from Equations (12.5) gives αx = αy = 3.30 × 10–6/°C This value is in reasonable good agreement with those experimentally observed. Table 12.1 displays thermal expansion data for a carbon/epoxy [0/±60/0]s laminate with the following ply properties: E1 = 160 GPa α1 = 0.64 × 10–6/°C E2 = 9.2 GPa α2 = 28.1 × 10–6/°C ν12 = 0.33 G12 = 5.24 GPa The experimental and predicted coefficients of thermal expansion listed in Table 12.1 can be compared. It is observed that the data are reasonably consistent upon heating and cooling. The analysis somewhat underpredicts αx and overpredicts αy. Note also the significant anisotropy in thermal expansion for this lay-up. TABLE 12.1 Measured and Predicted Thermal Expansion Coefficients (in units of 10–6/°C for a [0/±60/0]s carbon/epoxy [IM6/3501-6] laminate) CTE Measured Predicted αx 1.97 (H)a 2.04 (C)a 1.68 αy 3.15 (H) 3.41 (C) 3.94 a H and C represent heating and cooling, respectively. TX001_ch12_Frame Page 166 Saturday, September 21, 2002 5:05 AM © 2003 by CRC Press LLC
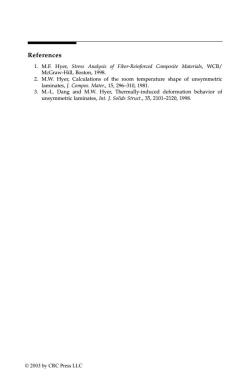
References 1.M.F.Hyer,Stress Analysis of Fiber-Reinforced Composite Materials,WCB/ McGraw-Hill,Boston,1998. 2.M.W.Hyer,Calculations of the room temperature shape of unsymmetric laminates,J.Compos.Mater.,15,296-310,1981. 3.M.-L.Dang and M.W.Hyer,Thermally-induced deformation behavior of unsymmetric laminates,Int.I.Solids Struct.,35,2101-2120,1998. ©2003 by CRC Press LLC
References 1. M.F. Hyer, Stress Analysis of Fiber-Reinforced Composite Materials, WCB/ McGraw-Hill, Boston, 1998. 2. M.W. Hyer, Calculations of the room temperature shape of unsymmetric laminates, J. Compos. Mater., 15, 296–310, 1981. 3. M.-L. Dang and M.W. Hyer, Thermally-induced deformation behavior of unsymmetric laminates, Int. J. Solids Struct., 35, 2101–2120, 1998. TX001_ch12_Frame Page 167 Saturday, September 21, 2002 5:05 AM © 2003 by CRC Press LLC
按次数下载不扣除下载券;
注册用户24小时内重复下载只扣除一次;
顺序:VIP每日次数-->可用次数-->下载券;
- 《纺织复合材料》课程参考文献(Experimental Characterization of Advanced Composite Materials, Third Edition)10 Lamina Thermoelastic Response.pdf
- 《纺织复合材料》课程参考文献(Experimental Characterization of Advanced Composite Materials, Third Edition)09 Lamina Off-Axis Tensile Response.pdf
- 《纺织复合材料》课程参考文献(Experimental Characterization of Advanced Composite Materials, Third Edition)08 Lamina Flexural Response.pdf
- 《纺织复合材料》课程参考文献(Experimental Characterization of Advanced Composite Materials, Third Edition)07 Lamina Shear Response.pdf
- 《纺织复合材料》课程参考文献(Experimental Characterization of Advanced Composite Materials, Third Edition)03 Processing of Composite Laminates.pdf
- 《纺织复合材料》课程参考文献(Experimental Characterization of Advanced Composite Materials, Third Edition)02 Analysis of Composite Materials.pdf
- 《纺织复合材料》课程参考文献(Experimental Characterization of Advanced Composite Materials, Third Edition)01 Introduction.pdf
- 《纺织复合材料》课程参考文献(Computational Materials Science,From Basic Principles to Material Properties)11 Integration of Modelling at Various Length and Time Scales.pdf
- 《纺织复合材料》课程参考文献(Computational Materials Science,From Basic Principles to Material Properties)09 Molecular Dynamics Simulations in Biology, Chemistry and Physics.pdf
- 《纺织复合材料》课程参考文献(Computational Materials Science,From Basic Principles to Material Properties)08 Magnetism, Structure and Interactions at the Atomic Scale.pdf
- 《纺织复合材料》课程参考文献(Computational Materials Science,From Basic Principles to Material Properties)06 Symmetry Properties of Electronic and Photonic Band Structures.pdf
- 《纺织复合材料》课程参考文献(Computational Materials Science,From Basic Principles to Material Properties)05 Simulation of Active and Nonlinear Photonic Nano-Materials in the Finite-Difference Time-Domain(FDTD)Framework.pdf
- 《纺织复合材料》课程参考文献(Computational Materials Science,From Basic Principles to Material Properties)04 A Solid-State Theoretical Approach to the Optical Properties of Photonic Crystals.pdf
- 《纺织复合材料》课程参考文献(Computational Materials Science,From Basic Principles to Material Properties)02 The Essentials of Density Functional Theory and the Full-Potential Local-Orbital Approach.pdf
- 《纺织复合材料》课程参考文献(Computational Materials Science,From Basic Principles to Material Properties)01 Introduction.pdf
- 《纺织复合材料》课程教学资源(书籍文献)Composites forming technologies(Edited by A. C. Long).pdf
- 《纺织复合材料》课程参考文献(Composite materials science and applications,Second Edition)08 Thermal Properties.pdf
- 《纺织复合材料》课程参考文献(Composite materials science and applications,Second Edition)07 Electrical Properties.pdf
- 《纺织复合材料》课程参考文献(Composite materials science and applications,Second Edition)06 Tailoring Composite Materials.pdf
- 《纺织复合材料》课程参考文献(Composite materials science and applications,Second Edition)05 Materials for Lightweight Structures, Civil Infrastructure, Joining and Repair.pdf
- 《纺织复合材料》课程参考文献(Experimental Characterization of Advanced Composite Materials, Third Edition)13 Open-Hole Tensile and Compressive Strengths of Laminates.pdf
- 《纺织复合材料》课程参考文献(Experimental Characterization of Advanced Composite Materials, Third Edition)14 Characterization of Delamination Failure.pdf
- 《纺织复合材料》课程参考文献(Experimental Characterization of Advanced Composite Materials, Third Edition)Appendix A Compliance and Stiffness Transformations and Matrix Operations.pdf
- 《纺织复合材料》课程参考文献(Experimental Characterization of Advanced Composite Materials, Third Edition)Appendix B Preparation of Test Specimens and Panels.pdf
- 《纺织复合材料》课程参考文献(Experimental Characterization of Advanced Composite Materials, Third Edition)Appendix C Sample Laboratory Report.pdf
- 《纺织复合材料》课程参考文献(Experimental Characterization of Advanced Composite Materials, Third Edition)Appendix D Unit Conversions.pdf
- 《纺织复合材料》课程参考文献(Experimental Characterization of Advanced Composite Materials, Third Edition)Table of Contents.pdf
- 《纺织复合材料》课程参考文献(Computational Mechanics of Composite Materials)01 Mathematical Preliminaries.pdf
- 《纺织复合材料》课程参考文献(Computational Mechanics of Composite Materials)02 Elasticity Problems.pdf
- 《纺织复合材料》课程参考文献(Computational Mechanics of Composite Materials)03 Elastoplastic Problems.pdf
- 《纺织复合材料》课程参考文献(Computational Mechanics of Composite Materials)04 Sensitivity Analysis for Some Composites.pdf
- 《纺织复合材料》课程参考文献(Computational Mechanics of Composite Materials)05 Fracture and Fatigue Models for Composites.pdf
- 《纺织复合材料》课程参考文献(Computational Mechanics of Composite Materials)06 Reliability Analysis.pdf
- 《纺织复合材料》课程参考文献(Computational Mechanics of Composite Materials)07 Multiresolutional Wavelet Analysis.pdf
- 《纺织复合材料》课程参考文献(Computational Mechanics of Composite Materials)08 Appendix.pdf
- 《纺织复合材料》课程参考文献(Computational Mechanics of Composite Materials)Contents.pdf
- 《纺织复合材料》课程参考文献(Fiber-Reinforced Composites,THIRD EDITION)Contents.pdf
- 《纺织复合材料》课程参考文献(Fiber-Reinforced Composites,THIRD EDITION)01 Introduction.pdf
- 《纺织复合材料》课程参考文献(Fiber-Reinforced Composites,THIRD EDITION)02 Materials.pdf
- 《纺织复合材料》课程参考文献(Fiber-Reinforced Composites,THIRD EDITION)03 Mechanics.pdf